Industrial bucket elevators
Bucket elevators transfer product simply and reliably with minimal footprint area. Gough’s Swinglink® elevator systems use a continuous line of swinging pendulum buckets to transfer large volumes of product. You can arrange the systems in many different layouts to deliver product where you need it — delivering free flowing material from one location to another, with no product degradation.
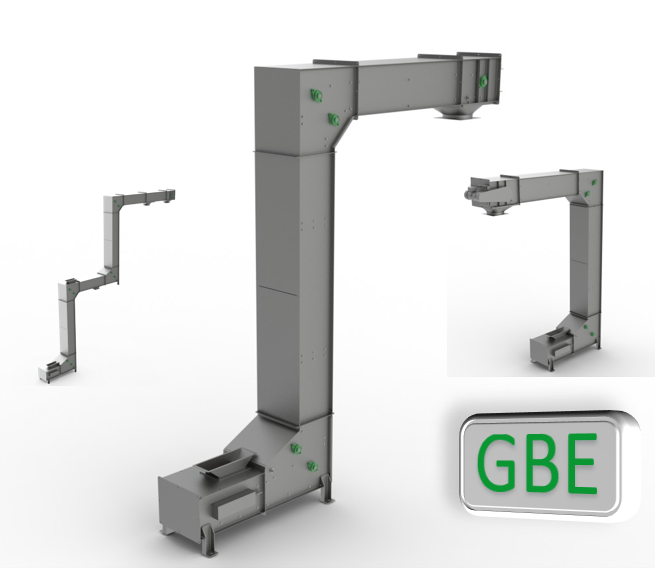
Introduction
The Gentle Handling Solution
The Gough Swinglink® Bucket Elevators use a patented design to move products in open buckets from one point to another.
Product is static in the bottom of the bucket throughout the process, which removes the possibility of damage during travel. A line of buckets moves past a spot where workers add product, and the workers fill each bucket partially. Two chains move the buckets through the bucket circuit.
We also supply bucket conveyors, a horizontal version with no vertical sections.
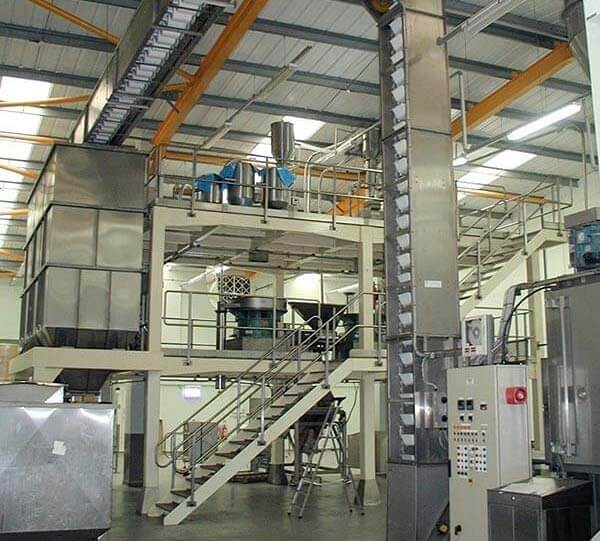
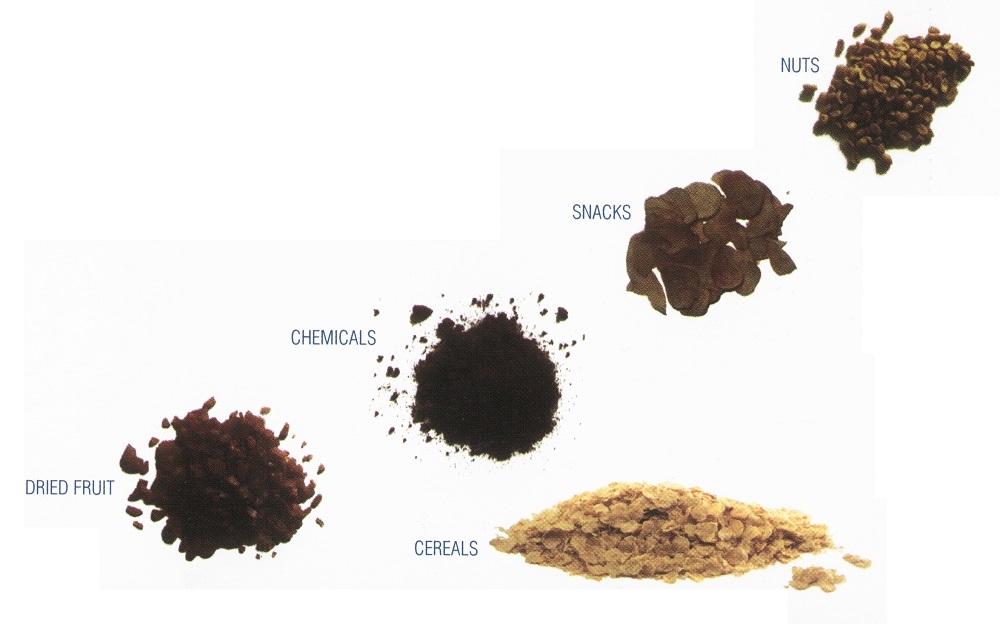
How it works...
Feeding
Product feeding into the elevator can be from a single or multiple entry points. Bucket design overlaps, so no material spillage, but if there is, trays can be incorporated.
The Transfer
Once product is in the bucket, it is protected without degrading all throughout the transfer route. Smooth and reliable motion from the boot section (lower), verticals and final upper sections.
Discharging
Discharging product from the buckets can occur at a single end tipping action or across multiple, individually controllable tipping points onto different product lines such as different big bags or a packing line.
Tailored design
The configurations are boundless, with many configuration (shape) designs to suit your production layout. The elevator is a superb, efficient and non-degrading conveying technique used in many industries.
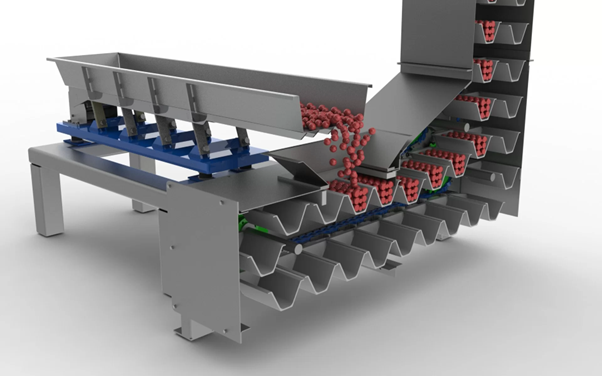
Key advantages of the Swinglink Elevator
Delicate
We achieve gentle handling of delicate materials to maintain product integrity, from abrasive and coarse aggregates and minerals.
Drive position
A drive system positioned near the ground, rather than on the upper section for easy of access.
Easy clean
There is easy tray removal through streamlined system integration. It provides optional viewing ports and detachable panels upon request.
Buckets
It uses a patented bucket design to ensure the dependable delivery of your materials. Food Grade Polypropylene, metal detectable polymer or stainless / carbon Steel
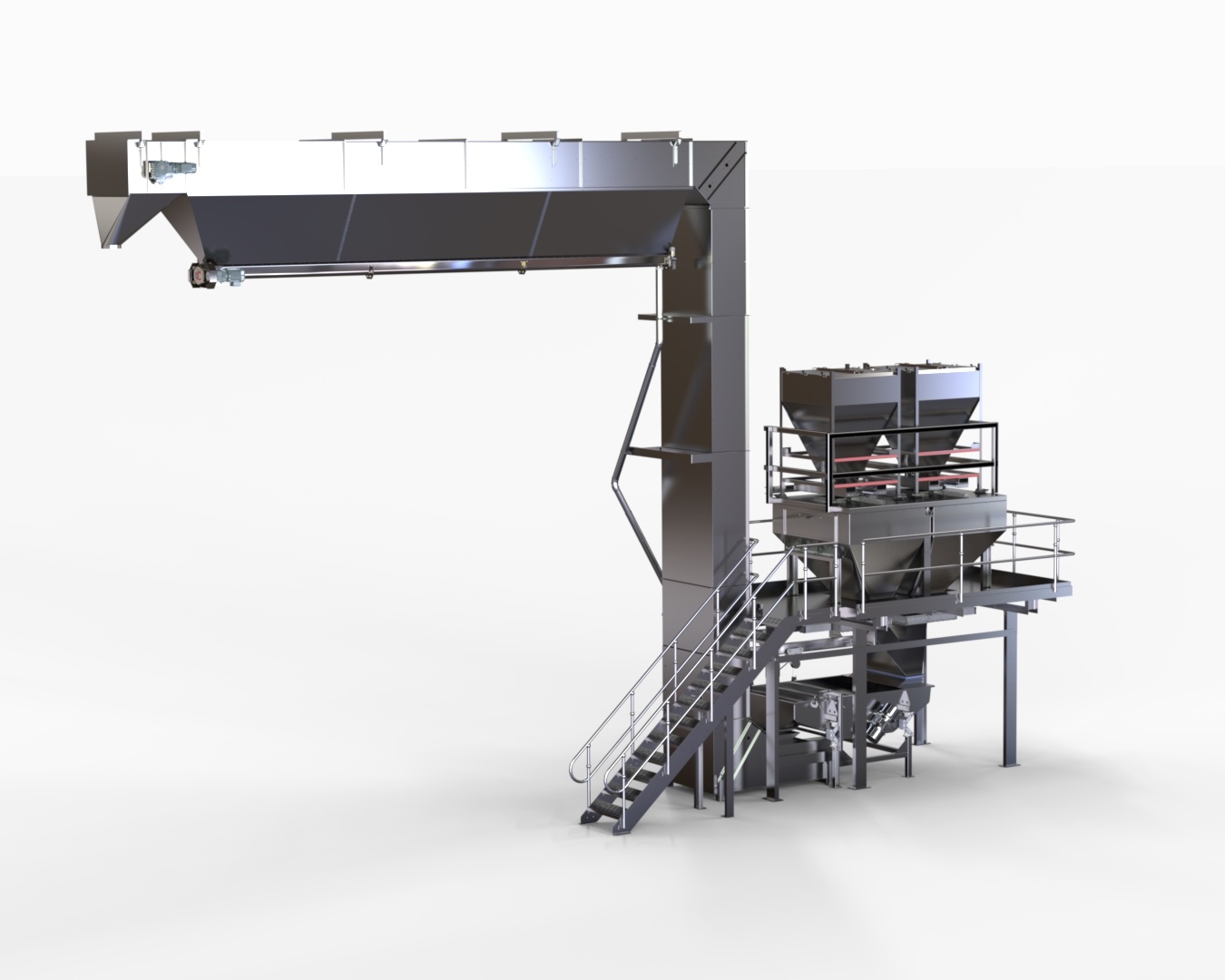
Design Options
Gough can design the elevator system in many configuration shapes:
- J, Z, true Z or vertical, T, C
- incline
- incline horizontal
- loop systems
- stair/step configuration for up or down
- straight horizontal
-
Gough Swinglink® bucket elevators use pendulum buckets that swing freely during travel.
-
The product rests safely in the bottom of the buckets, ideal for handling friable products gently.
-
The control panel mounted inverter supplies motors with variable speed and variable torque safety control.
- If you need an elevator with mobile capabilities this can also be supplied.
- You can create any setup to move things. It can move materials or components not only from one place to another, but also around other objects or production systems.
- You can also develop these configurations for multiple inlet and discharge positions and even a travel/ adjustable discharge position.
- One system can incorporate multiple inlet and multiple discharge points, joining or splitting product streams as needed.
- You can easily remove and replace buckets by hand without tools, for fast cleaning during change over operations. You can replace 100 buckets in less than 20 minutes.
-
The chains are a patented design fitted with roller arms to carry the elevator buckets. Shafts and sprockets link the chains, coordinating the movement of the chain and keeping the buckets in line and parallel.
Enhancements...
Reality Cases & Articles
From the history archives, we can refer to many different success stories of how our machines have helped industry.
For each of the core products, we provide a bit more insight on our designs and how the solution helped a company face production issues of quality, production throughputs, reliability and product flexibility.
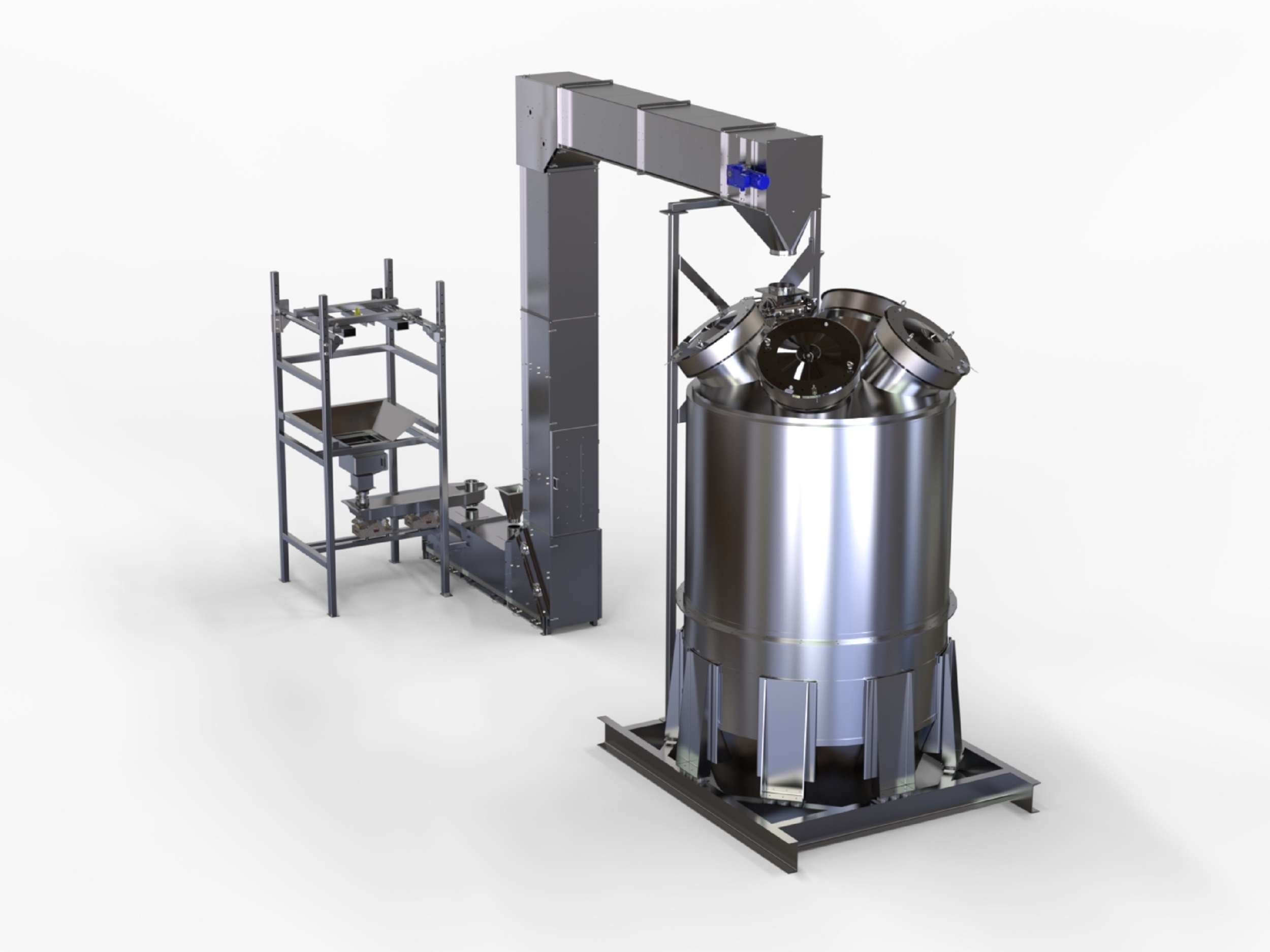
What Advantages Do Pendulum Bucket Elevators Have Over Other Conveying Methods?
Pendulum bucket elevators are designed to provide mainly continuous vertical and horizontal conveying...
Flipbook for sieves
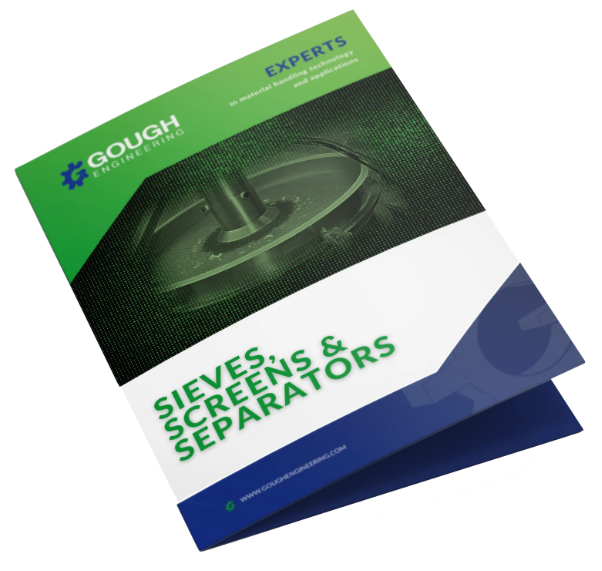
Flipbook for Transfer Systems
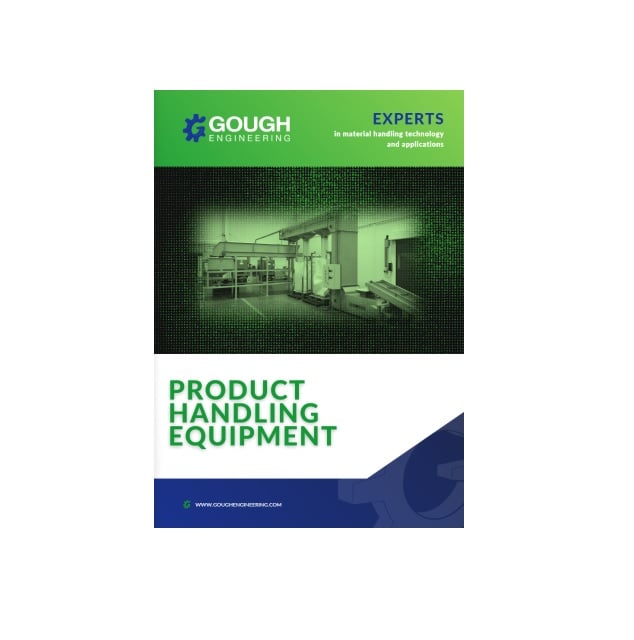
Contact us today
Want to find out more on our superb patented Swinglink Elevator and all its benefits...
Call our sales team to discuss your requirements on:
+44 (0)1782 567770
or via email contact@goughengineering.com
Q & A
Here are a few questions and answers and we are always available to call and discuss you application specifics.
How is a bucket elevator driven?
The Swinglink bucket elevator can be driven using one, efficient motor. The superb design used over decades by our customers, use sprockets and chains to pull the buckets through the configuration design.
How do the bucket tip?
You can have a single end-over tipping arrangement where the product falls out of the bucket rotating around the final sprocket. Or pneumatic tips can be controlled for multiple discharge points.
What parts are available?
All Gough Swinglink elevator parts are available, where bucket stocks are kept and managed at Gough Engineering for fast response if you have any breakages.
Can I have Gough service the elevator?
Gough Engineering provide all types of servicing services to our customers. From simple health checks, to full modifications servicing and component replacements. All these can be prioritised according to your production maintenance schedules and we will work with you for minimal disruption.
Can I modify an elevator?
Modification can be made such as reducing or extending elevator sections. This would mean altering the chain lengths, but modifications are reviews and assessed to guide you all the way to resolve any future additional requirements in the elevator design to meet your demands.
Are there option on material construction?
Yes, we can accommodate and supply the elevator with powder coated panels and framework. Or other options include, stainless-steel 304, Makrolon panels, wire mesh panels and many more options.