Product Conveying Schemes
At Gough Engineering we provide our customers with comprehensive support and guidance through the entire process of a conveying scheme, from conception to installation.
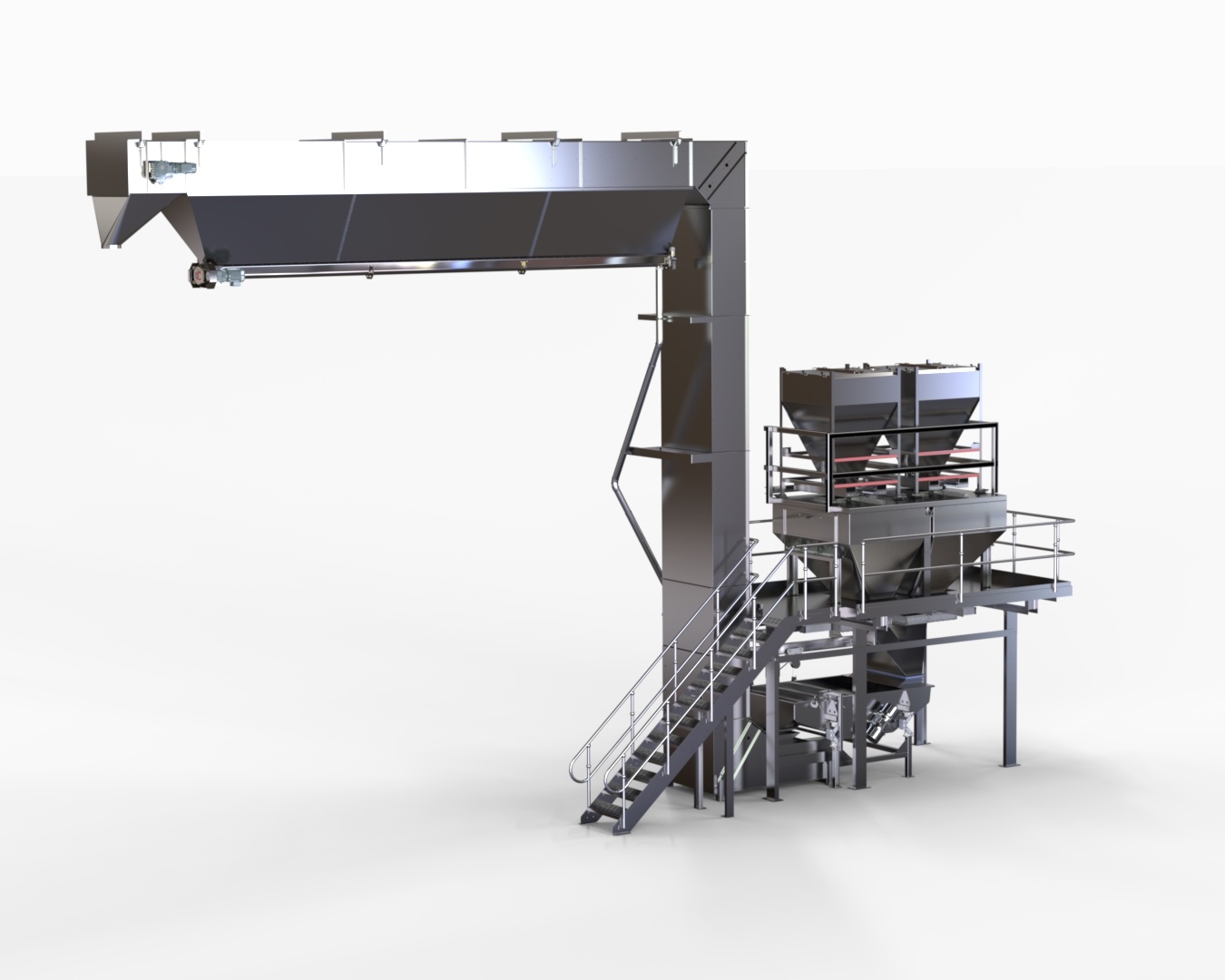
.
Solutions & Expertise In-house
Our dedicated team ensures a seamless experience, offering expertise and assistance, promising equipment reliability and maintenance assistance.
Gough Engineering’s priority is to act in our customers’ best interest, to develop long-term relationships built on trust.
As part of our conveying system design, we align it with your specific requirements. This approach not only addresses the various challenges that may occur in production processes, but also aims to enhance overall efficiency and productivity on the production line.
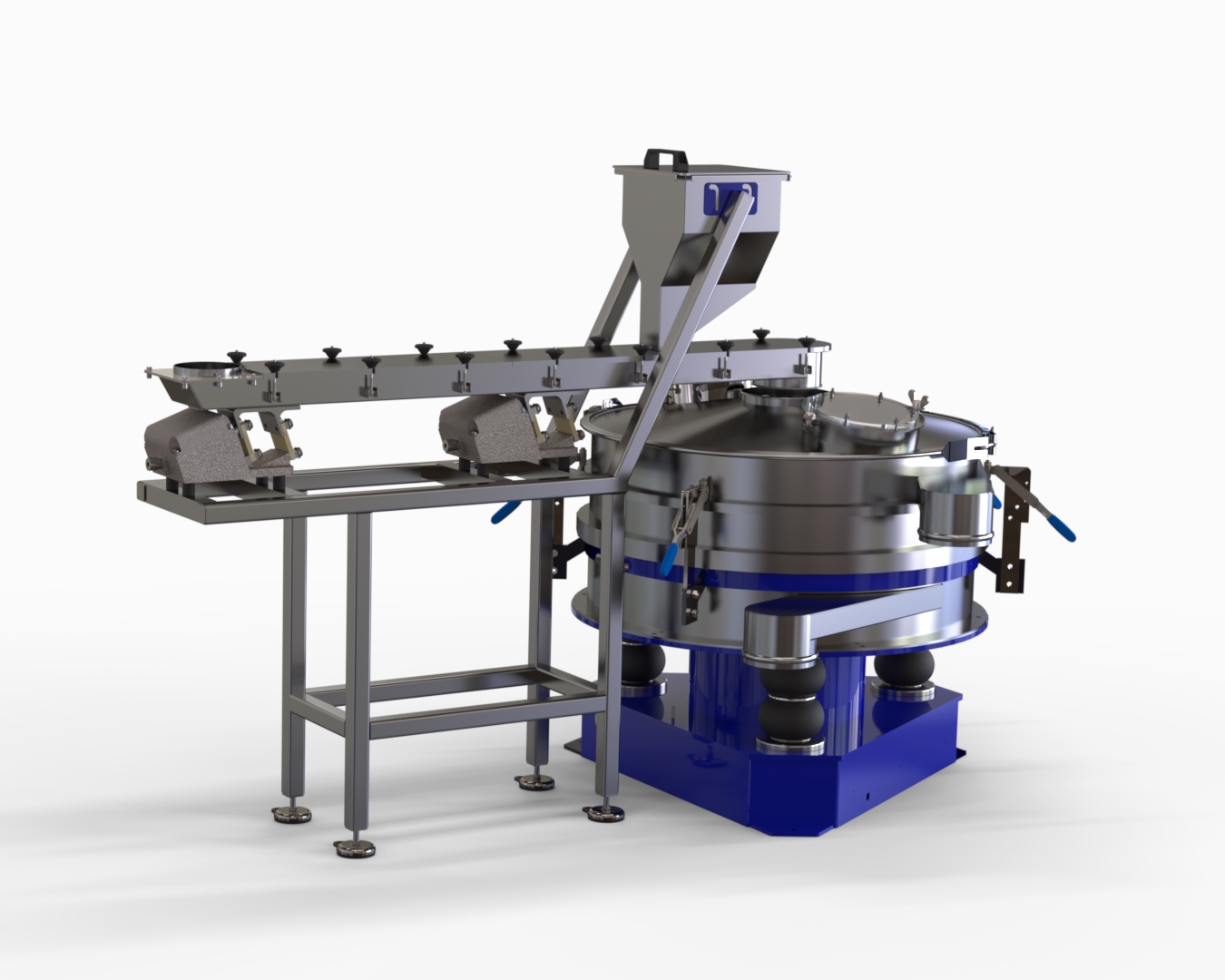
Assurance
We check all equipment thoroughly for quality and test it before delivery. We also provide factory acceptance testing and a mechanical installation service. Lastly, we provide a brilliant after-sales support service, as well as a parts and maintenance facility.
More reliable equipment
We ensure consistent and trouble-free operation over the long term. This reliability translates to reduced downtime and maintenance, contributing to sustained productivity.
Less energy consumption
Our conveying systems save energy and lower costs for our clients.
Less cleaning requirement
The thoughtful integration of features and materials minimises the collection of debris and facilitates easier cleaning processes, streamlining maintenance efforts.
Less product spillage
Less manual handling
The integration of automation and precision in our designs significantly reduces the need for manual handling.
Integration Examples
There can be a range of different equipment combinations within a product conveying scheme.
Screening systems to guarantee product quality, or transfer equipment such as elevators or feeding equipment, might be used. Depending on your requirements, we can support the controlled distribution of product within your processes.
Gough Engineering supports with:
- Smaller schemes
- Vacuum or aero-mechanical conveying solutions
- Bucket elevators for delicate handling and segregated distribution/feeding
- Multiple long elevator runs in both horizontal and vertical planes
Gough Engineering’s systems support precise quality control from production to final packing lines — even road tankers.
Let’s look at some examples of different setups with classification and elevation:
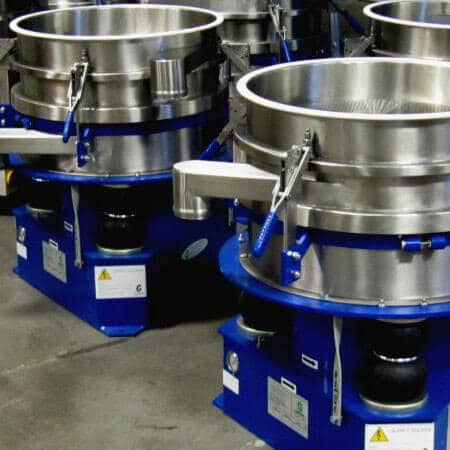
Stations
Product contents are removed from small bags of up to 25 kilograms (kg) using a rip and tip station design. Various scheme combinations are available; for example, you can incorporate de-dusting with extraction, additional magnets for steel capture, elevation using vacuum or aero-mechanical means and simple check screens to separate and classify the materials according to your production needs.
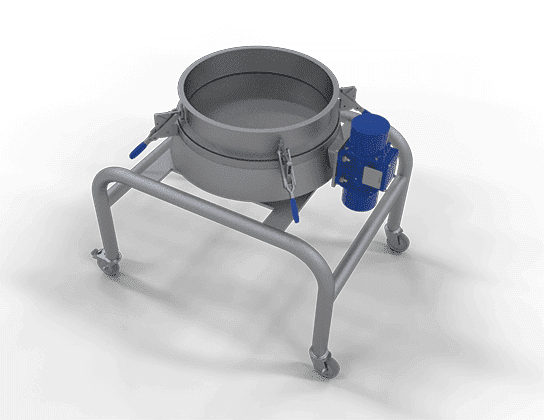
Basic Rip & Tip station
To the right, you can see a stainless steel, food grade rip and tip station with pivoting hood and built in vibration check screen for any debris or contaminates removal. Benefits of this station include:
- Straightforward design
- Easy to clean
- Pivoting hood with extraction points
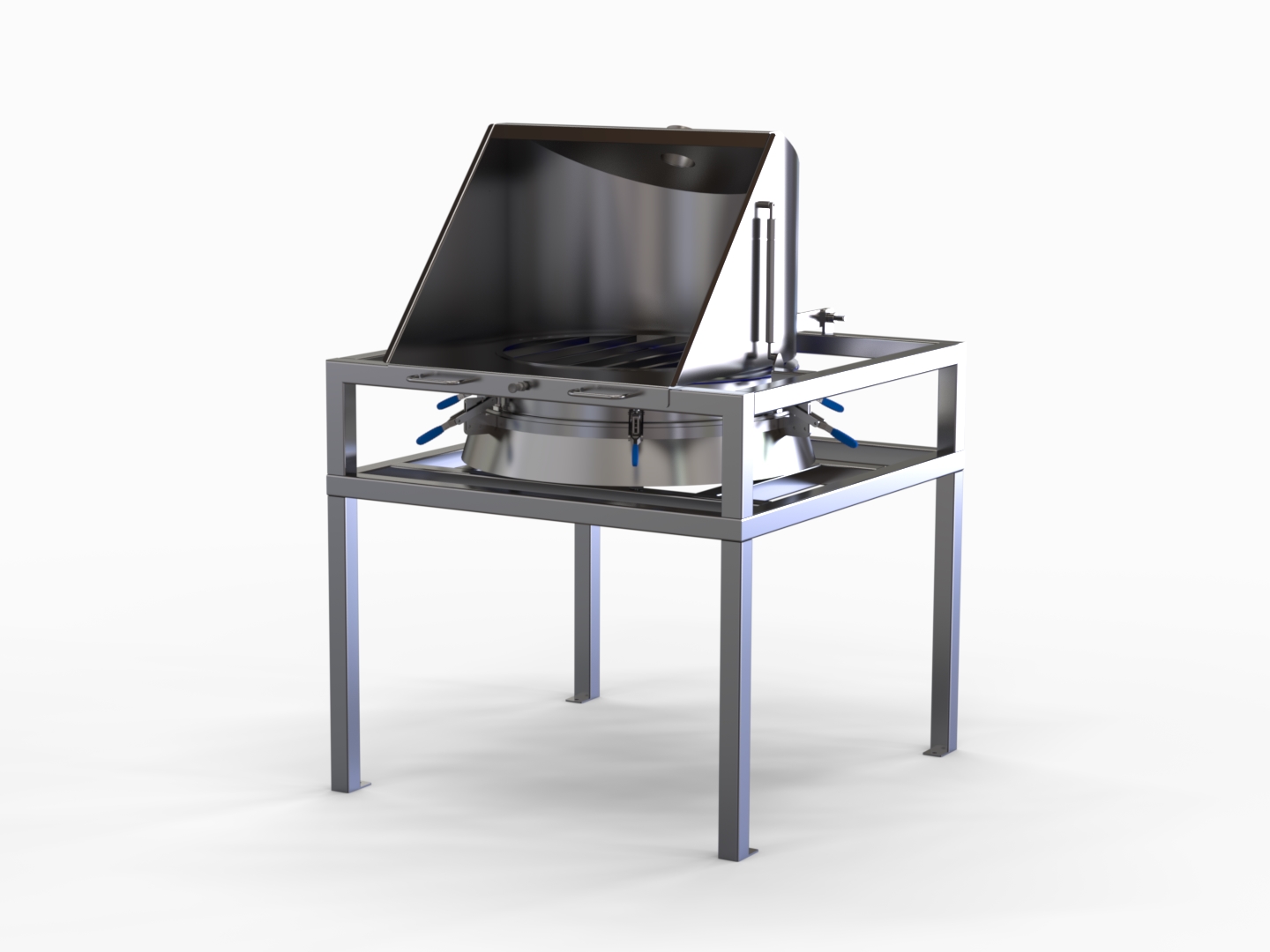
Rip and tip to larger vessels with check screening
To fit larger receiving bins or vessels, we can create a rip and tip station for operators to safely discharge bagged product with integrated screening. The unit pictured to the left shows support side panels to fit to existing extraction during operational de-dusting. It includes:
- Combined steps and hood
- Accommodation of larger receiving vessel heights under sieve
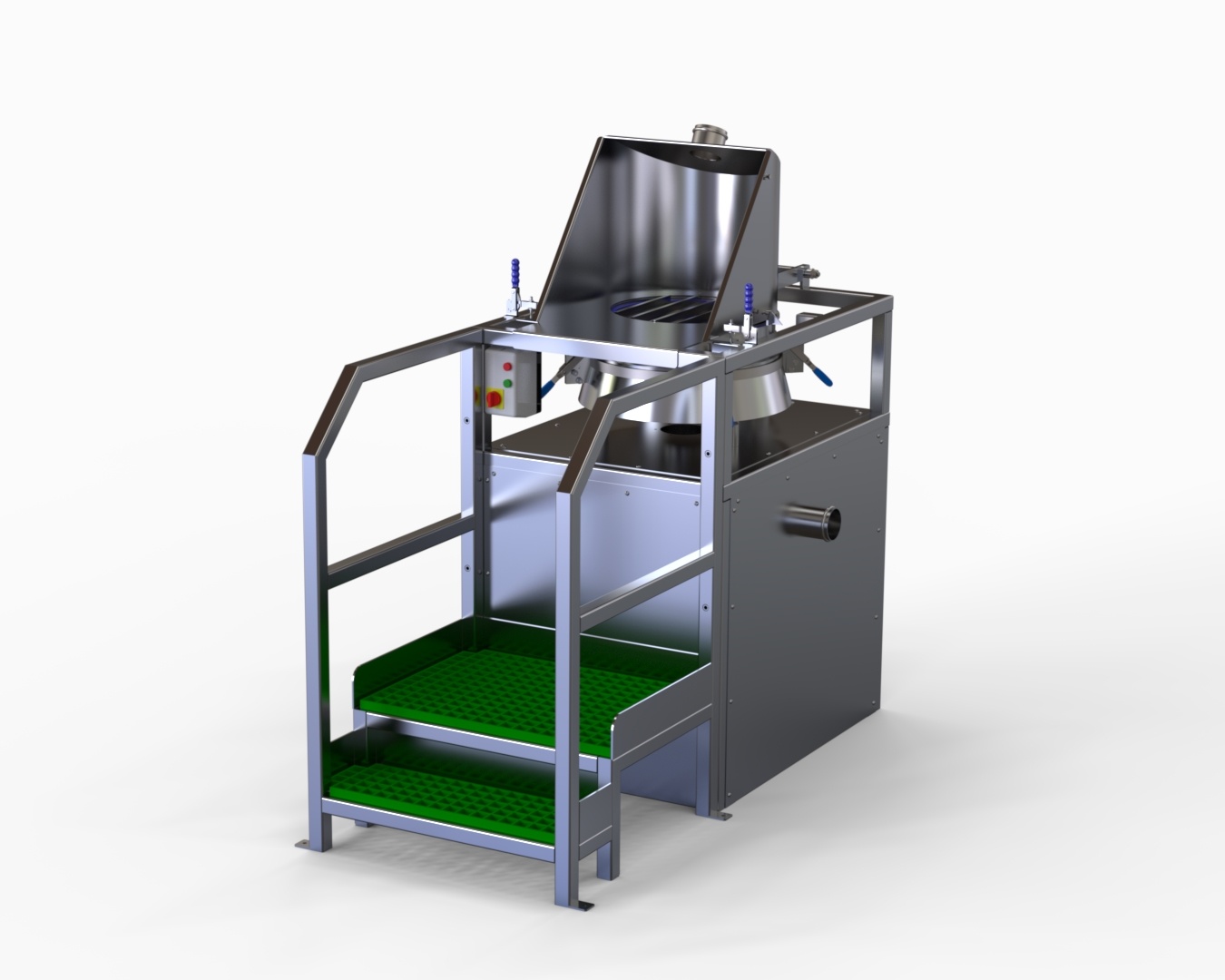
Feeding and screening integration
To the right we have a mobile food grade small receiving stainless-steel hopper and vibratory feeder using electro-mechanical drives to generate excellent product feed delivery to the next process. The feeding and screening unit features:
- Efficient electro-magnetic drive
- Variable speed control
- Suitable for any product in food, plastics, pharma and chemicals
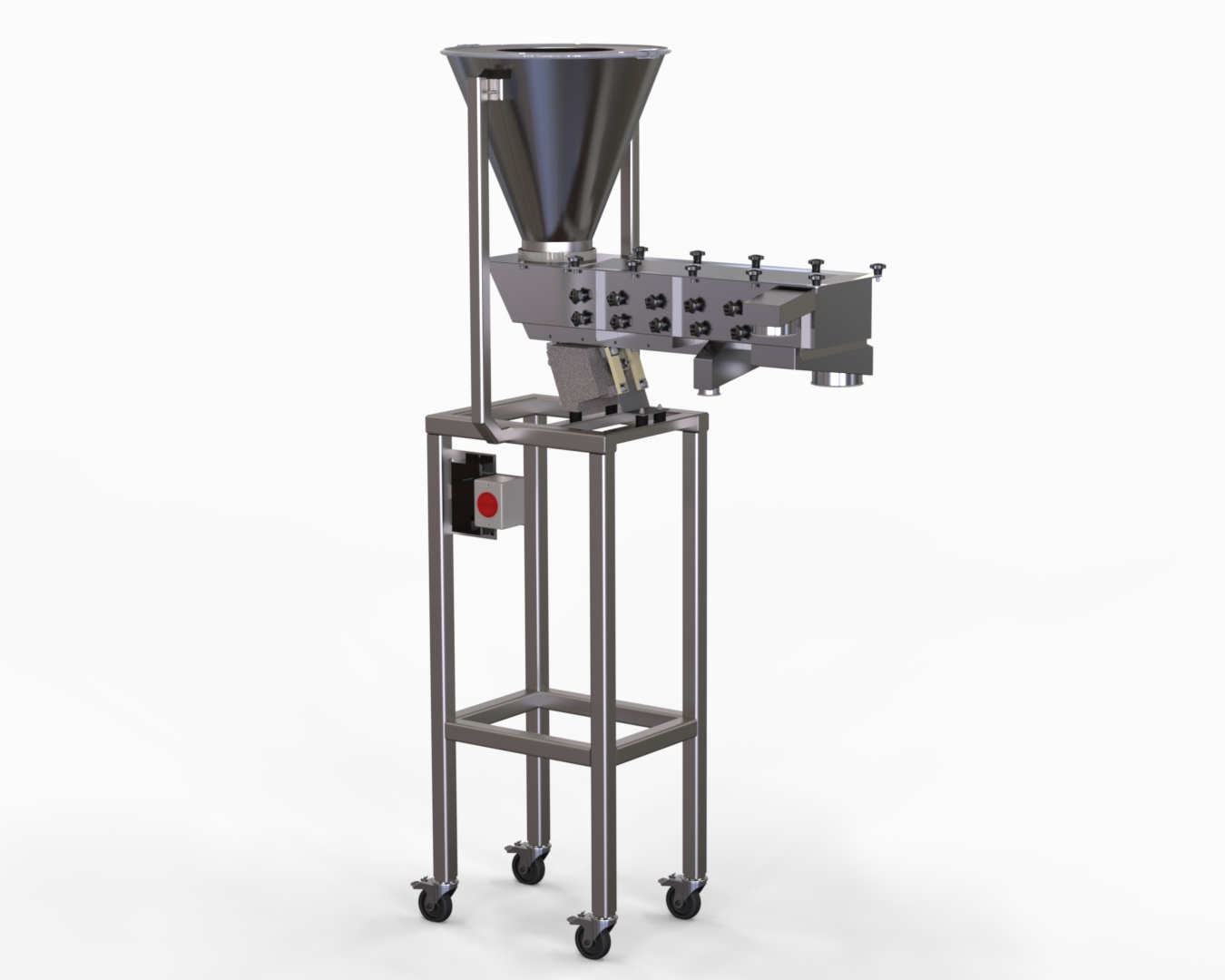
Feeding to a classifier
Here’s another example on the left showing a vibratory E-mag feeder, delivering product to a Vibrecon separator, classifying product into three fractions for further processing. This unit promises:
- Consistent product flow
- Integrated separator
- Multiple fraction classification
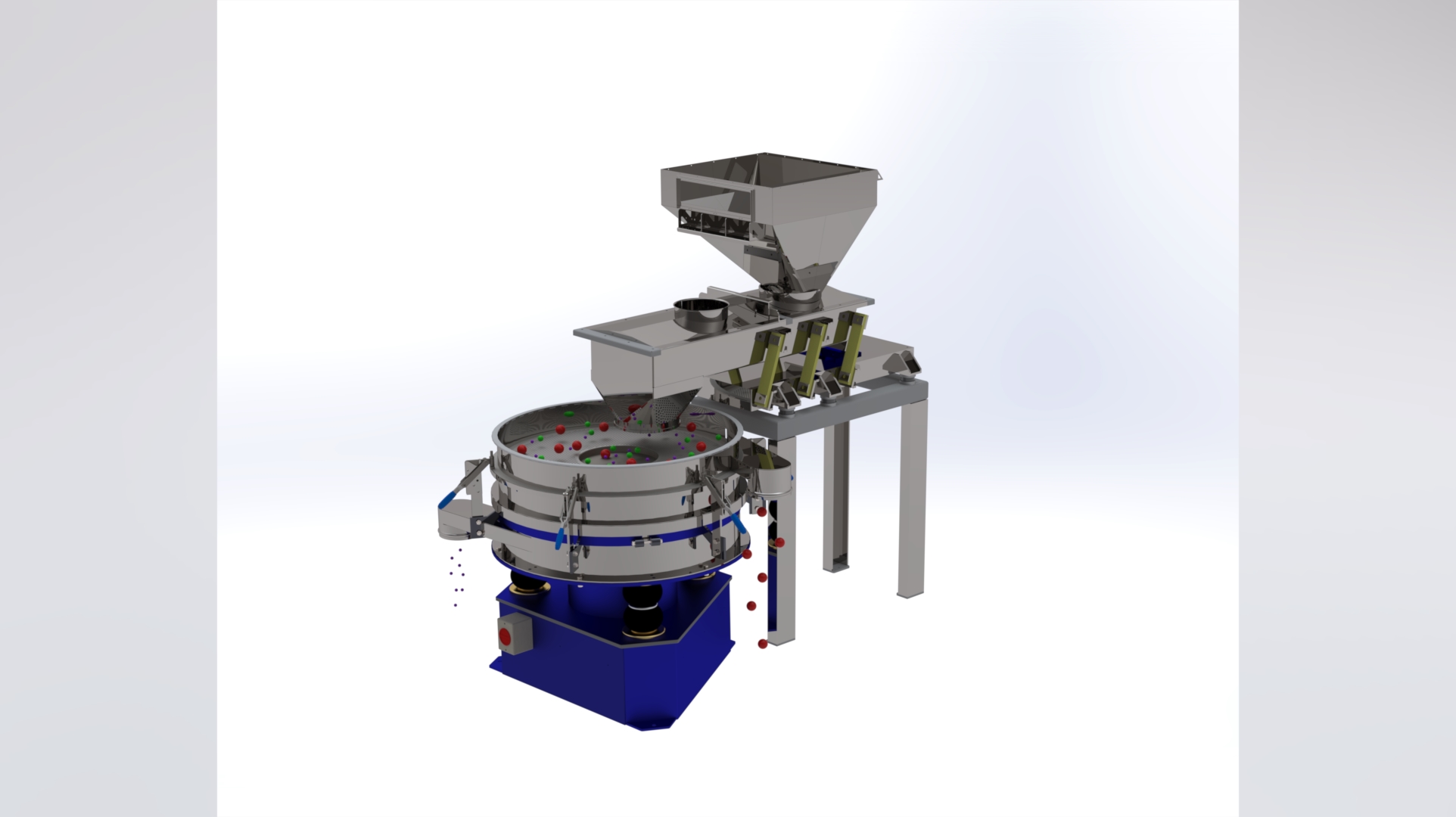
Rip&Tip with check screen and Elevation
You may need to rip and tip small product bags, remove any debris or contaminates with a vibrational check screen and elevate up to a blender — as shown on the left. This solution may include:
- Mobile unit
- Extraction connected hood
- Fast product elevation
To maintain cleanliness, you can use a rip and tip station equipped with a large quality control vibration screening unit. This setup also includes a built-in extraction/filter unit, as shown in the image on the right with a pivoting hood. This setup may include:
- Larger 850 mm screen
- Fully integrated filter extraction
- Built in screening
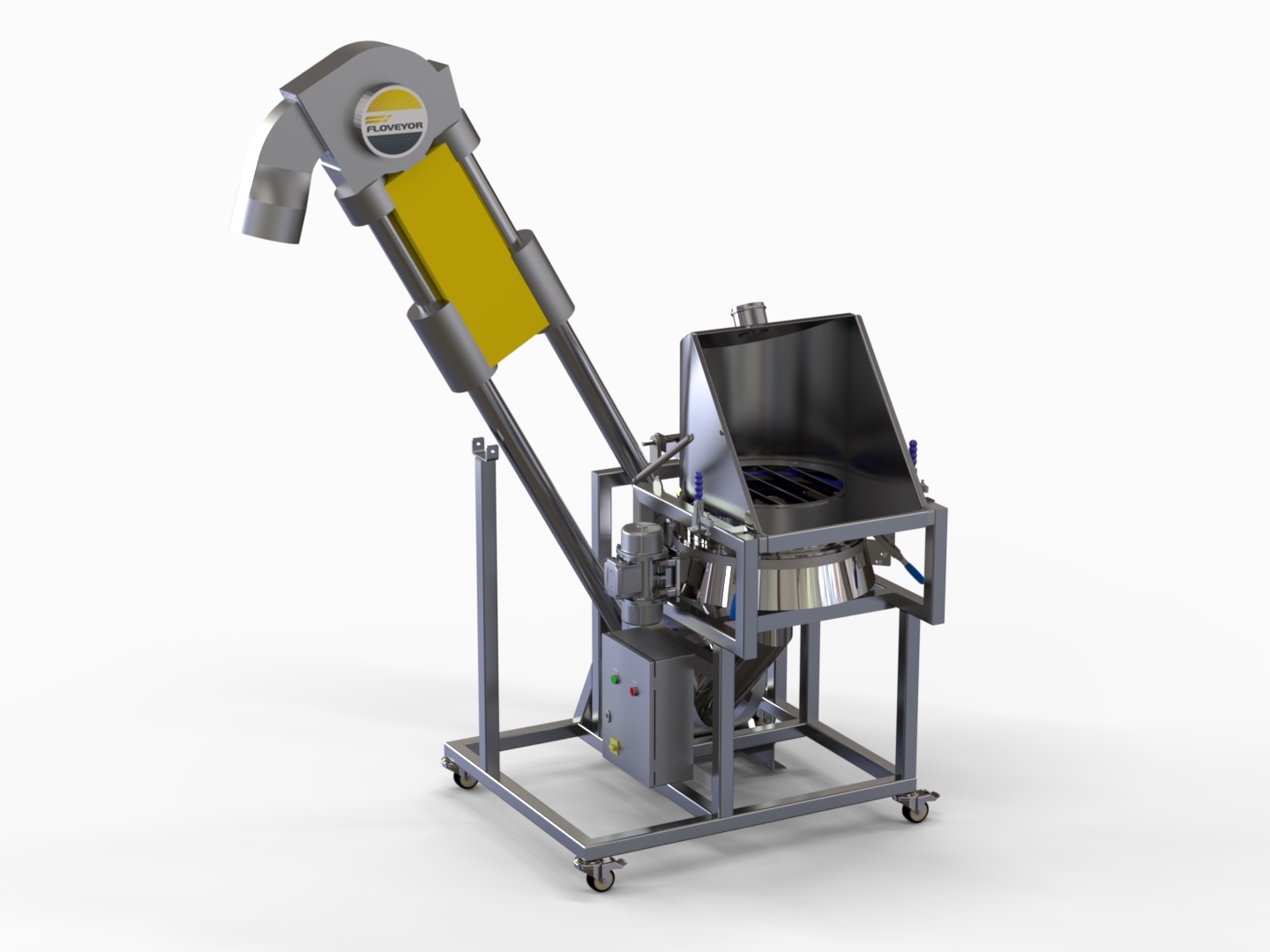
Now for something bigger...
Gough big bag systems
Efficiently handle bulk materials from big bags using a Gough Big Bag (GBB) discharger. This FIBC ‘Big Bag’ discharger system can be operated with a forklift cruciform or hoist/pendant. It includes a combined vibratory feeder along with an additional small bag rip & tip station. This setup is uniquely tailored to fit your building logistics. It can come with:
- Hoist or forklift big bag loading
- Integral small bag rip and tip station
- Feeding into one destination
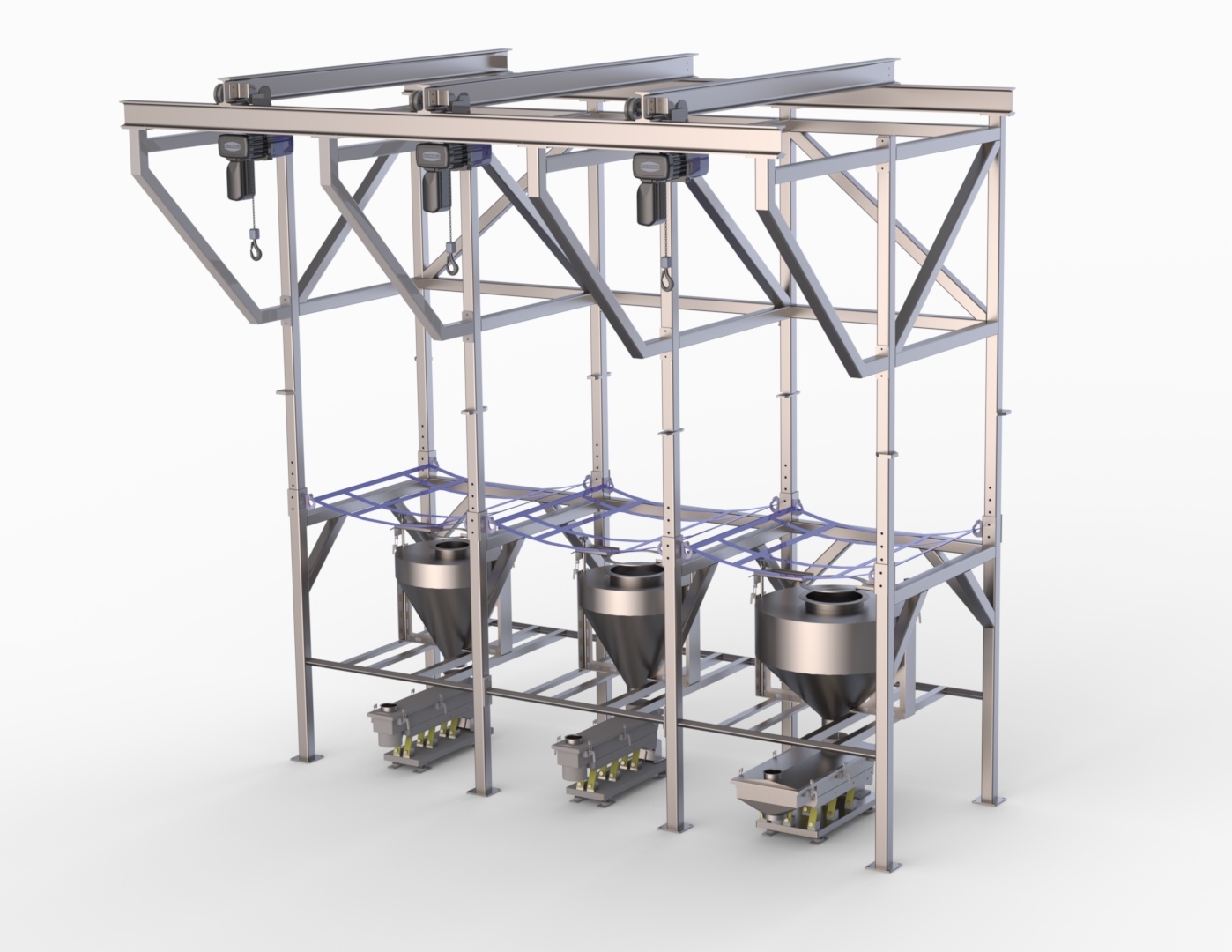
Bulk handling with elevation and integrated quality control
The example on the right shows a Big Bag discharging station with an untie chamber, control feeder leading to a Gough Vibrecon classifier, integrated to bucket elevator for final packing automation.
- Big Bag Discharge with Unite Chamber
- Integrated Quality Screening
- Full Bucket Elevator to next process
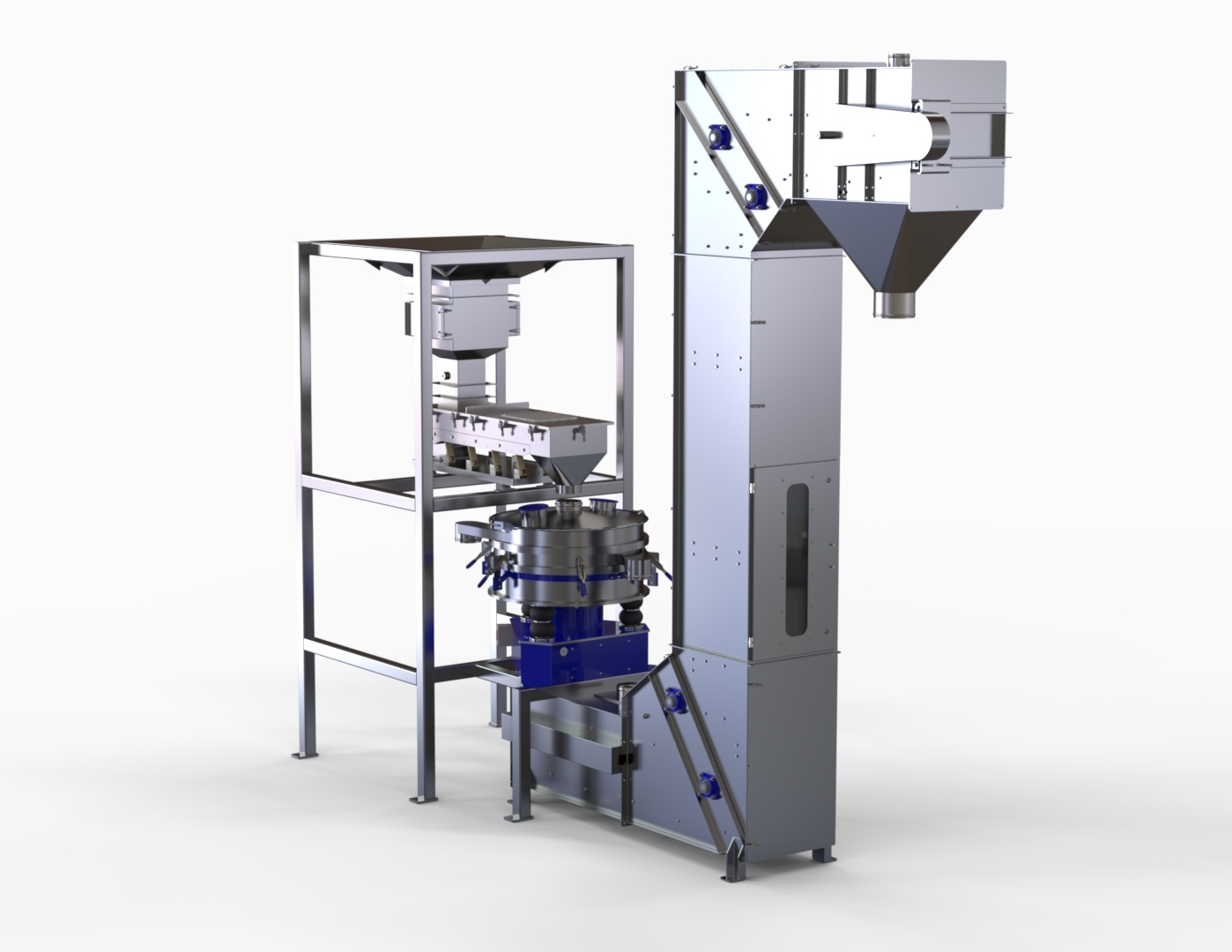
Big Bag discharge, through elevating elevator and into silo
This solution depicts the big bag discharging system with untie chamber feeding material directly into a vibrating feeder, smoothly delivering product into the feed end of the bucket elevator.
The bucket elevator will then elevate the product material up to the required height and discharge into the large silo, accompanies with explosion proof baffles.
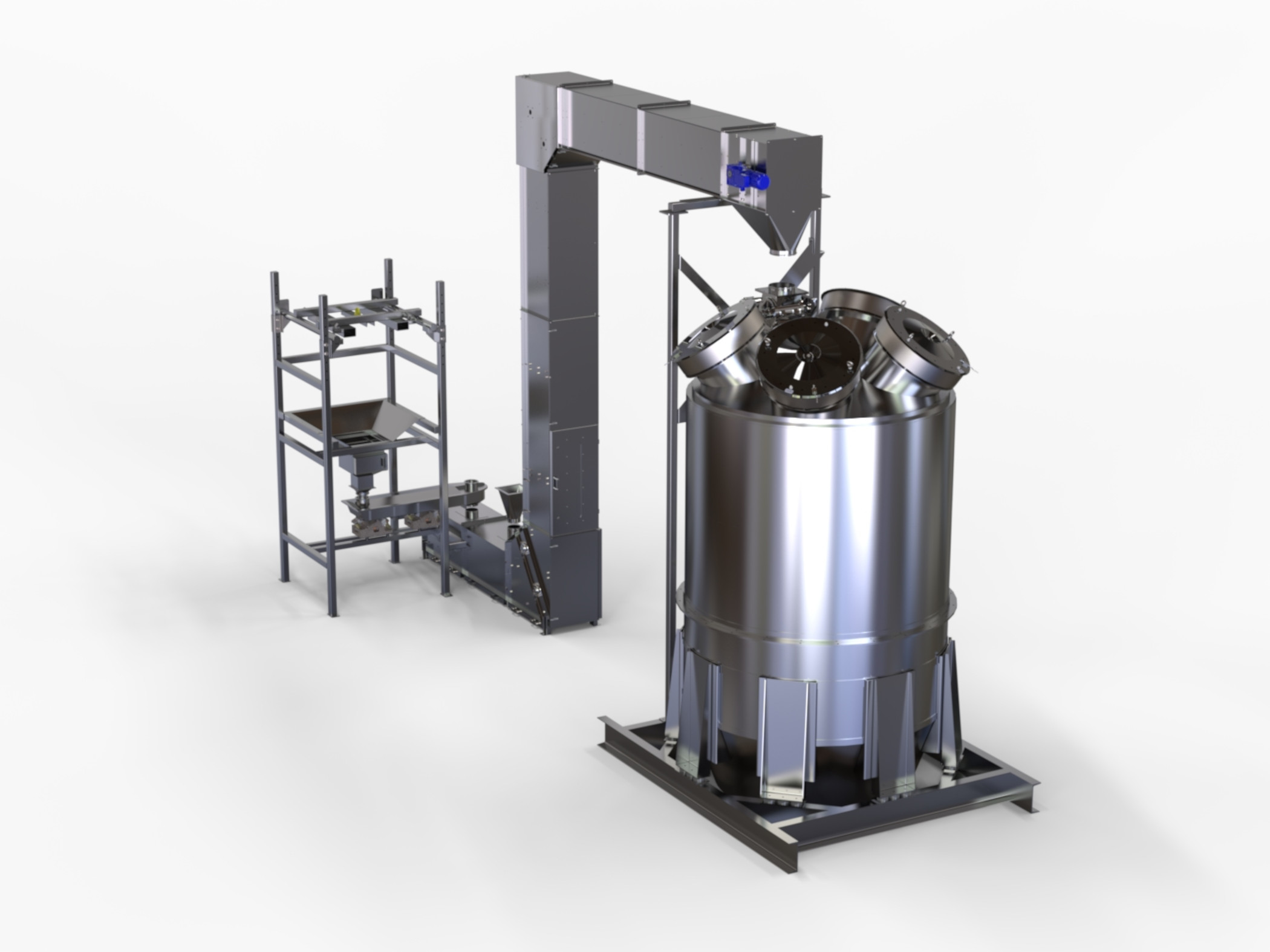
Road tanker loader
Tanker loading systems need to be designed for efficient product transfer from big bags or in-line conveying through to the road tanker and their related sizes (height, capacity, number of ports etc)
We design transfer systems with stringent control systems with volume high transfer capabilities - reaching 30 tons/hr with a twin set of units like the one pictures here.
- Big Bag discharger with paddle agitation
- Built in quality check screening
- Metal rejection system
- Strong, industrial design.
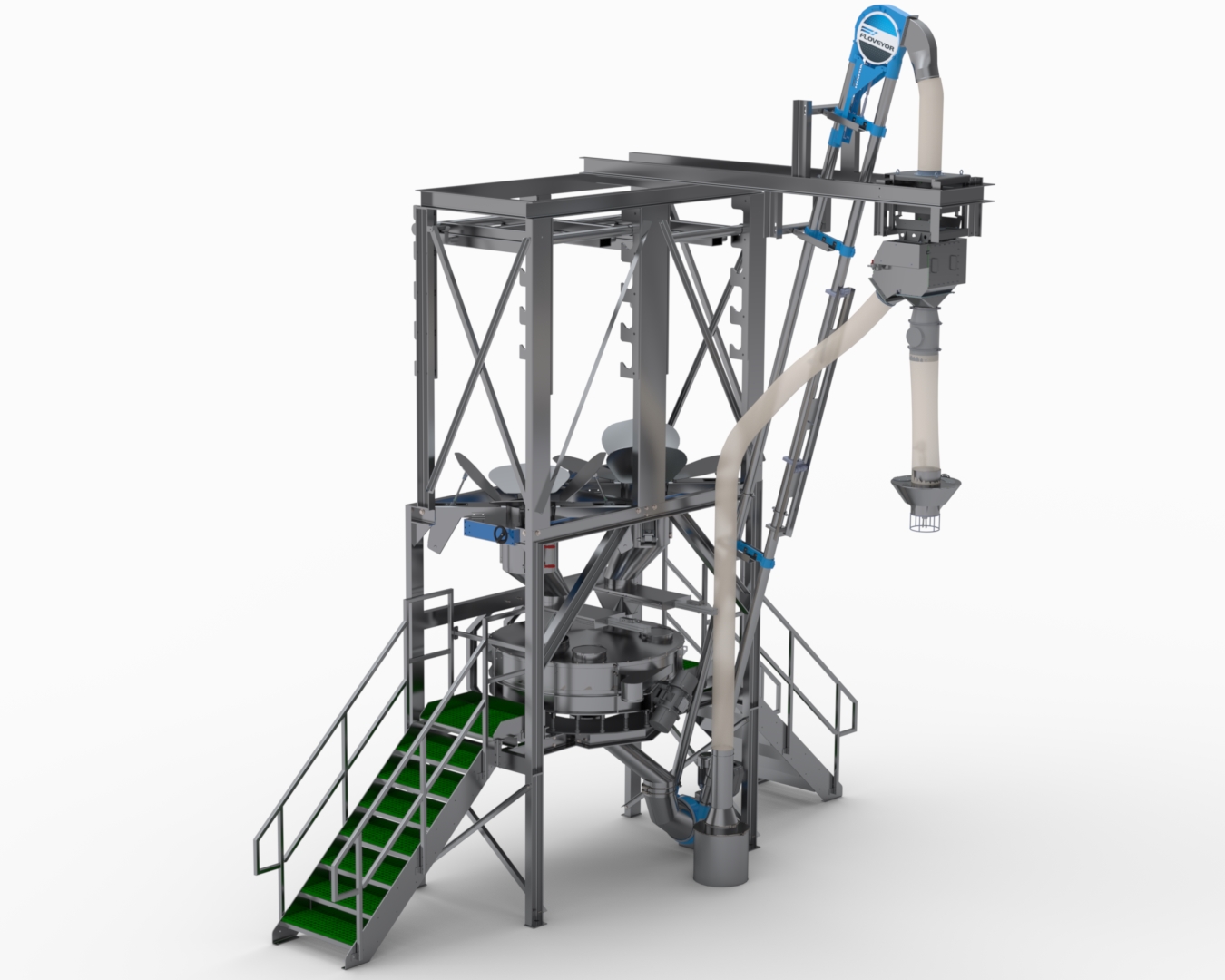
Checking screening before final packing
Lorem ipsum dolor sit amet consectetur adipisicing elit. Ab eligendi nemo quis dignissimos voluptatem itaque nobis. Cupiditate, eius. Provident animi culpa saepe velit, itaque maxime porro quaerat quam ratione expedita.
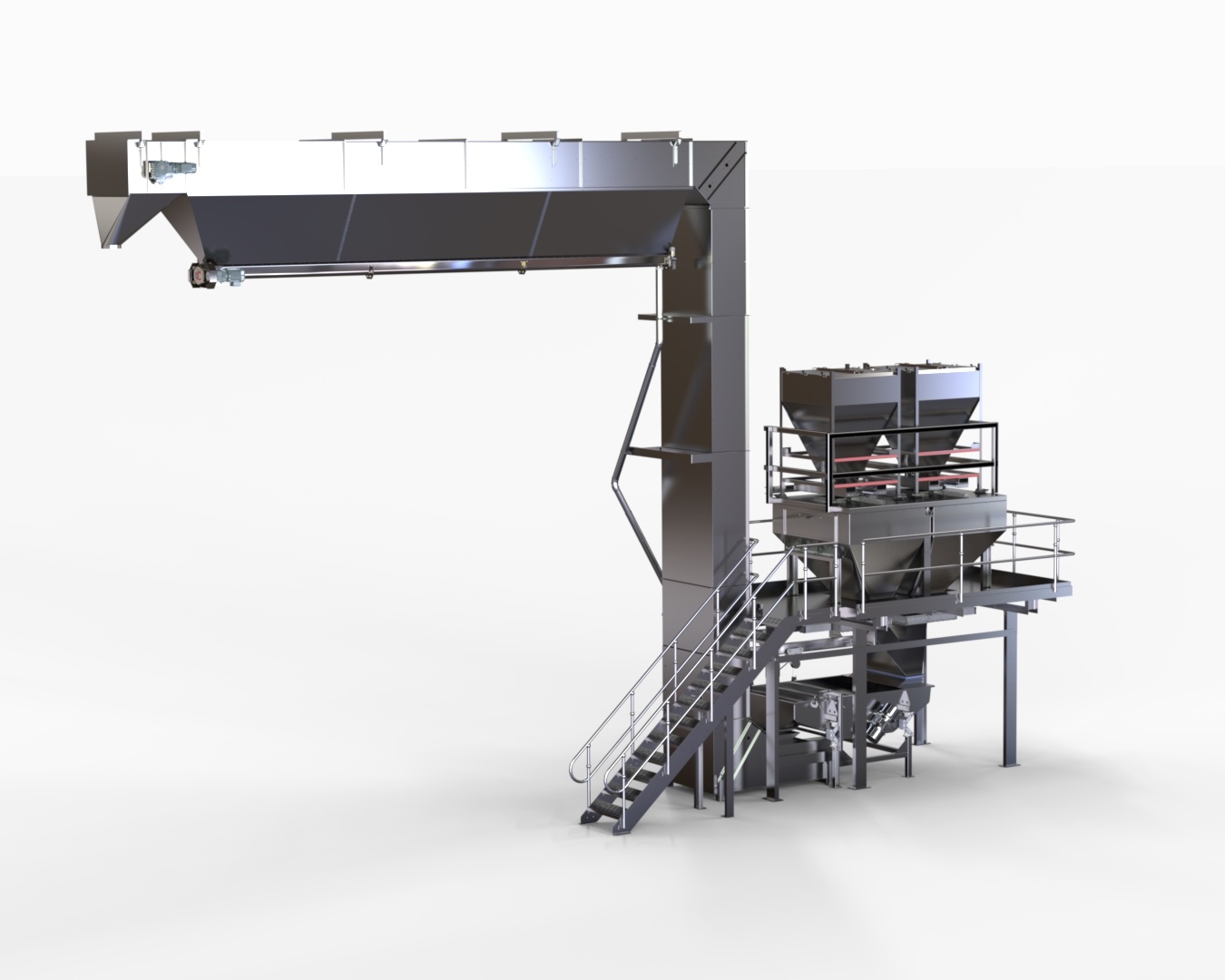
Whats next?
Gough Engineering has a unique ability to provide tailor made solutions.
Our standard range of machinery can be custom designed and adapted to your bespoke needs. Our specialists provide material handling solutions based on more than 70 years of engineering experience.
To gain a full understanding of your requirements, we conduct site visits, run trials with samples of your product, demonstrate equipment, exchange drawings and discuss similar projects we have completed. Once we have all the details, we supply a detailed offer and specification. Send an enquiry today and we will contact you to arrange a visit at your convenience.