Automation in chocolate food production is crucial to keep up with consumer demand. This particular case study relays how Gough Engineering designed and supplied the right elevator conveying equipment and screening solution for chocolate powder quality and material transfer management.
The Task
A well established chocolate powder manufacturer in North Wales required a conveying and powder screening system for the transfer of chocolate powder from production to packaging lines. It was important for the machinery to be cost effective and efficient.
For the screening, it was imperative to remove oversize particles, debris and conglomerates.
For the elevator, a smooth, gentle handling of the chocolate product when elevating and transferring from one location to another
What Was The Solution?
Gough supplied a Swinglink Bucket Elevator and Vibraflo Through Sieves. The Bucket Elevator is designed in a ‘Z’ shape design as a one-in-one-out unit. The Chocolate Drinking Powder enters the 9 inch (229mm) buckets at a rate of 4000kgs per hour. The standard enclosed painted mild steel casing shelters a 124 bucket series supported by a plastic chain network. Each elevator is powered by a 400V, 3 phase, 50 hertz electrical supply with a control panel included for basic operation requirements.
Once the Chocolate Powder reaches the end tip point of the bucket elevator it is then released into a stainless steel chute into a Vibraflo Through Sieve to be check screened before the powder is transferred to packaging. This seamless process means that the chocolate powder screening is able to take place quickly and efficiently, improving the quality of our client’s product.
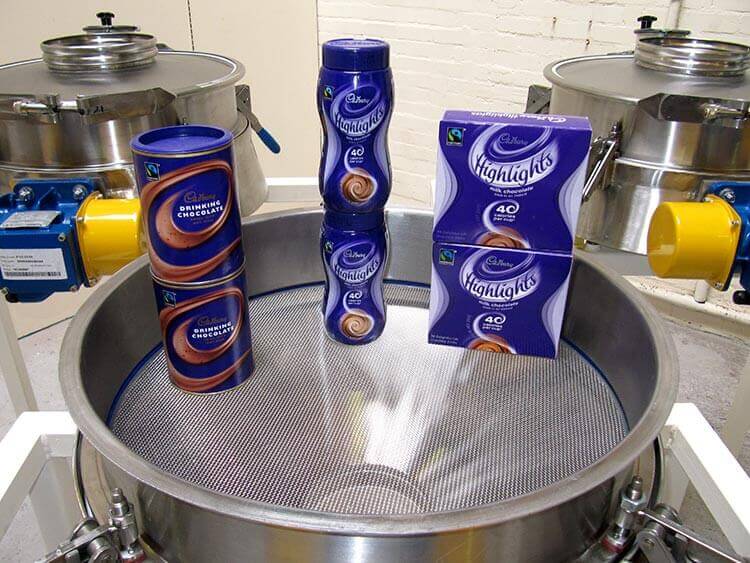
What Were The Final Results?
Gough’s energy efficient Bucket Elevators are designed to provide an effective, cost-efficient interface between process and packaging equipment. Gough systems are designed to ensure that all handling of product is undertaken using methods that are inherently gentle and cause minimum distress to the products being moved. This handling advantage provides a clear benefit in retain product quality compared to more aggressive handling by belt and bucket elevators
Gough has a long-standing relationship with the Cadbury / Kraft group and continue to provide efficient, reliable and cost-effective materials handling equipment to sites all over the world.
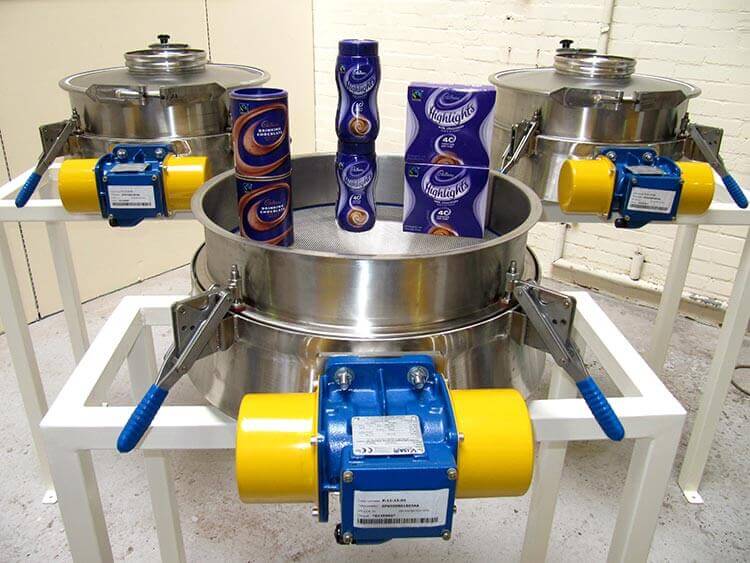
Related Products
Gough Batch Sieve (GBS)
The Gough Batch Sieve, supplied in 550mm and 850mm diameter screens and a core product in the sieving and screening range, provides a simple and robust method to check screen product using suitable stainless steel meshes with a given aperture. They are driven using a single motor mounted on the side of the sieve deck and are designed to be easily disassembled, cleaned and assembled again for minimum downtime. The batch sieve can be used in many industries, improving product quality effectively.
Gough Vibraflo (GVF)
The Gough Vibraflo (GVF), supplied in a range of sizes from 610mm to 1,372mm screen diameters, is a reliable and effective method of check screening both wet and dry products to remove lumps, oversize and contaminates which may be in the product material. The Vibraflo, just like to the batch sieve, flow the sieved material directly through the central part of the machine, automatically removing the oversize particles through a separate discharge spout. These units can be supplied with a support stand at any height to accommodate flow in your existing production line
Gough Vibrecon (GVC)
The Gough Vibrecon (GVC), supplied in a range of screen diameters from 610mm to 1,372mm is an all round performer, with the capability of having multiple screens (maximum of 3) within a single unit for multiple fraction classifications. The unit can have wire mesh or perforated plates or a mixture depending on application with many options including lids to retain dust, outlet spout designs, mobile castors and more,
Vibratory Feeder (GL:VF)
Vibratory feeders allow the controlled movement of product from one location to another using a single tray surface. The vibration can be generated by different drives and is normally required to generate a smooth continuous flow of material from one process to another. If the tray does have a scree built into the tray this would be called a vibratory screen.
Parts and Service
The parts and service department has always maintained an excellent client and customer relationship, bringing technical advise as well as the quick supply of spare parts from our in-house stock management.
Please contact us to discuss further...
If you'd like to find out more about our range of products and services, and how they can meet your requirements, then please contact us today.