Powders

Handling powders with a conveyor belt system
A range of different types of conveyor systems are available on the market. At Gough Engineering, we offer aero conveying, vibration and screw feeding options.
Aero-conveying leverages air currents to transport powders efficiently. Gough Engineering is the UK’s Floveyor partner, a company that solely develops aero-mechanical conveyor technology today. These systems provide a small equipment footprint capable of high throughputs, gentle transport of material, fully enclosed modular installations, minimal residue and easy-to-clean systems.
Vibration as a conveying mechanism uses oscillatory motions to convey powders. Vibrating conveyors offer advantages such as reduced maintenance, low noise levels, and precise control over material flow.
Screw feeding is another popular option and is particularly used for powders with varying consistencies, offering high efficiency and a continuous flow of materials.
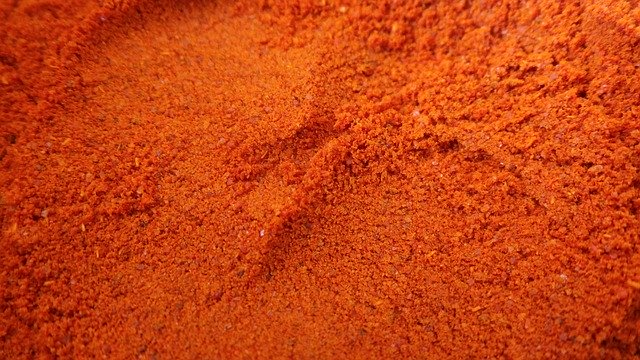
Dust emission control
A challenge tied to conveying powders, is managing and mitigating dust emissions.
To effectively address this challenge, covers can be placed on open systems, with gaps sealed as tightly as possible to reduce dust.
Another solution is adding extraction spigots to draw out as much dust as possible before it escapes. When including an extraction system, it can create a slightly negative pressure inside the system.
This negative pressure pulls in clean air through any openings and stops dust from getting out.
This means that, by covering and sealing gaps and using extraction spigots, you can effectively manage dust while keeping the environment cleaner and safer.
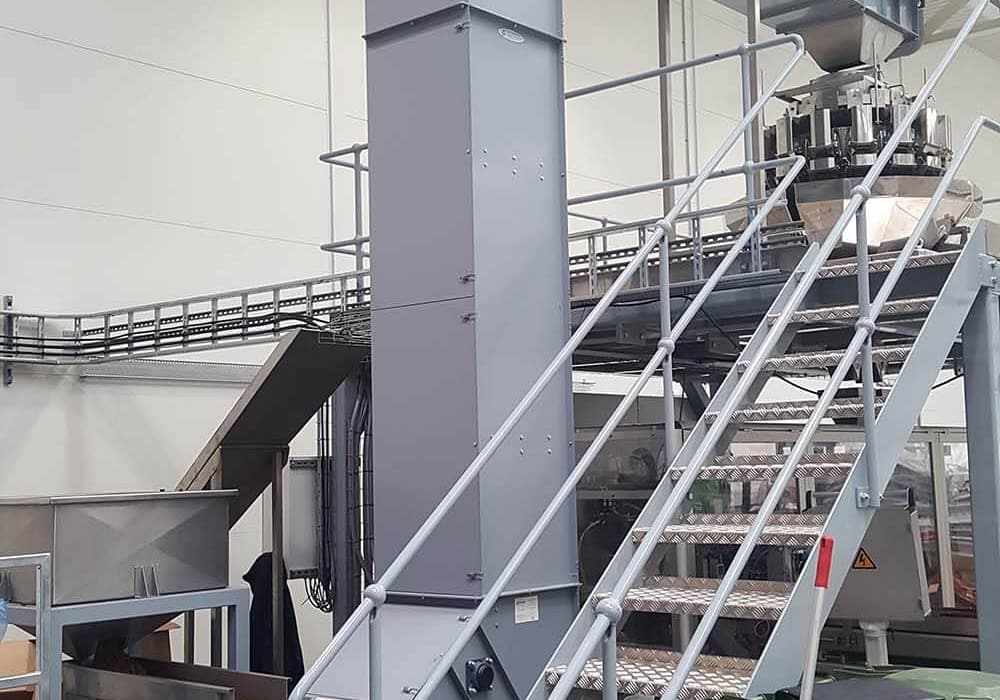
ATEX regulations
Connected to the challenge of managing powders, is the issue of ATEX compliance. ATEX regulations specifically address the risk of explosions caused by the build-up of dust and gas.
When dealing with equipment that handles powders, careful consideration must be given to how the risks of explosions can be controlled during the handling process.
A number of strategies can be employed to enhance safety. One effective method involves using electrical equipment designed to prevent dust from reaching electrical wiring. This preventive measure significantly reduces the risk of dust acting as a catalyst for electrical malfunctions.
It's also crucial to eliminate any potential sources of heat or sparks during the handling process, as these could initiate explosions.
Read more about material handling equipment in ATEX environments.
ATEX zone definitions must be clearly defined and submitted by the customer/client to Gough Engineering for equipment design assessment.
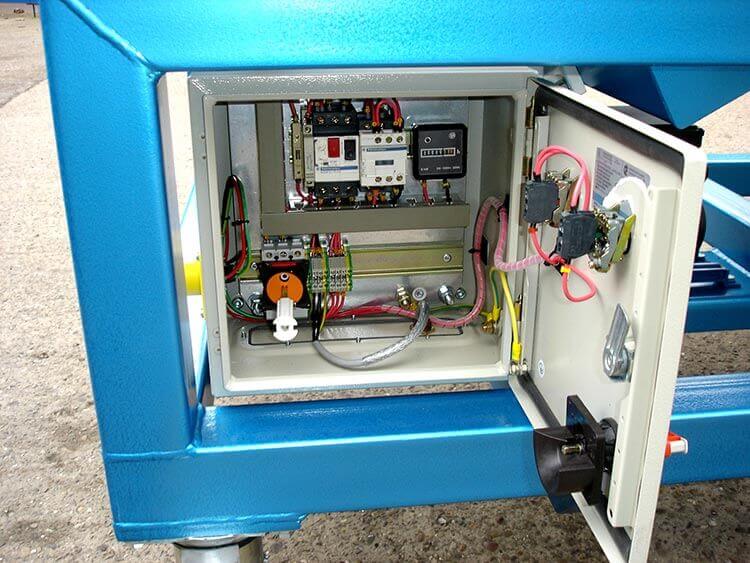
Equipment Selection
When choosing equipment for moving powders, tubular options stand out as highly effective.
Aero mechanical conveyors, tubular vibratory feeders and screw feeders are great choices as they facilitate the movement of the product through a tube.
Notably, the tube only has openings at its starting and ending points, serving as the inlet and outlet for the product as it enters and exits the system. This design ensures a contained and controlled process, making these equipment choices reliable and practical for conveying powders in various applications.
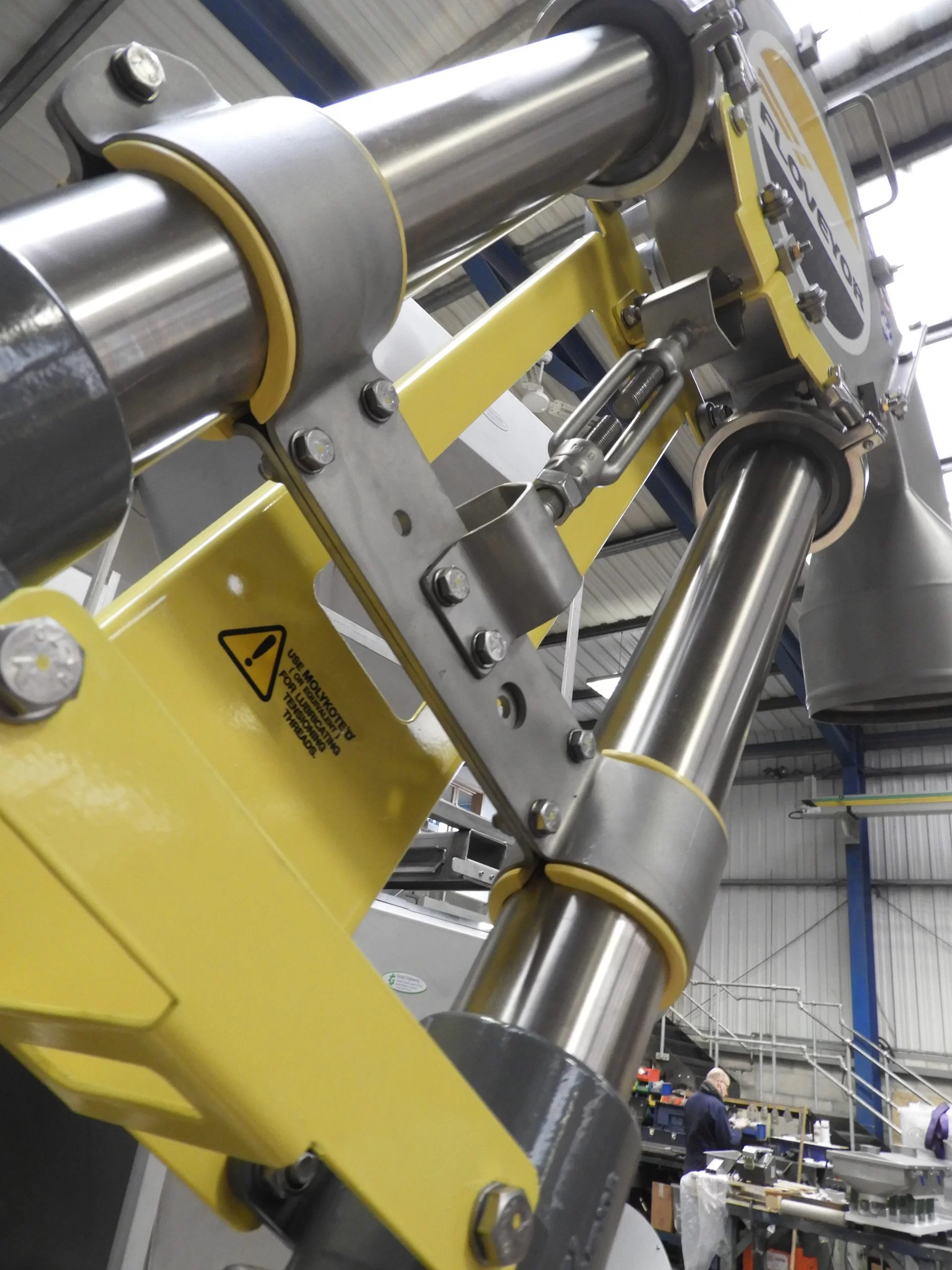
Equipment Cleaning
Cleaning equipment that has been in contact with powders can be difficult.
Accessing every nook and cranny to remove all traces of the previous product can be a labour-intensive task. Therefore, it's advantageous if the equipment system is designed with easy cleaning in mind.
Best practice is to minimise the presence of tight corners, maintain smooth surfaces and ensure convenient access to hard-to-reach areas.
These principles are best embodied in a tubular design, which proves to be an ideal choice. The characteristics of a tubular structure align with the best practices for equipment cleaning, facilitating a more straightforward and thorough cleaning process.
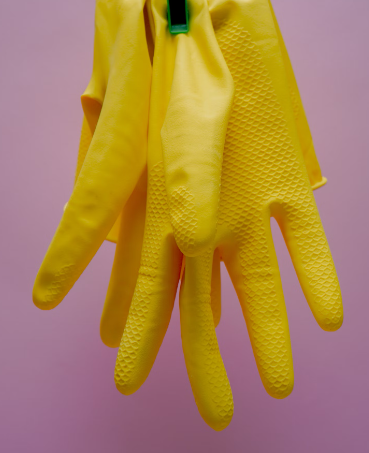
Contact today
Experts in food processing equipment for sieving, separating and transferring your food product safely and effectively.
Call our team of highly skilled engineers to discuss your requirements on 01782 567770 or online.