At Gough Engineering, we're proud to have continued our partnership with Lavazza, a leader in the coffee industry, by delivering cutting-edge bulk handling systems. In 2020, we provided Lavazza's Basingstoke, UK, facility with their first triple FIBC big bag discharging station.
In 2024, Lavazza returned to us for a second system for its production line — this time with a taller configuration demonstrating its confidence in our systems, engineering and service.
Big bag discharging system for powders and granules
Here’s a project overview of Gough Engineering’s supply of triple big bag discharging stations to Lavazza.
Materials handled:
- Various powders and granules
Application:
- Designed to handle large big bags, up to 1,500kg in weight
How it works:
- Loading the bag:
Big bags utilizing a cruciform and hoist/pendant solution are loaded into the big bag frame.
- Support & discharge:
The big bags are rested on a stainless steel chain support. The bags are then untied and the contents are discharged into a circular hopper secured by a clamp ring for smooth, enclosed transfer.
- Feeding process:
The hopper feeds the material into a vibratory feeder (GLVF) ensuring an even and controlled feed of the product with a top cover for protection and dust-free environment.
Custom-designed big bag discharger systems
The project’s scope involved the design, manufacture and full installation of three single big bag (GBB) discharger systems, which included:
- Triple GBB discharger frame: A single robust frame holding three individual discharging stations
- Dedicated components: Each station is equipped with its own cruciform position, hoist/pendant support chains, circular hopper and a dedicated vibratory feeder
- Enhanced height: The new system stands at an impressive height of 5,500mm to accommodate Lavazza's specific big bag needs
- ATEX-rated electric hoists: Ensuring safety and compliance, the electric hoists are ATEX rated
Project timeline
From initial design checks in May 2024, through drawing approval, to final delivery in August, Gough Engineering provided a seamless experience from concept to completion.
At Gough Engineering, we specialise in creating tailored bulk handling systems that meet the unique requirements of our clients.
Contact us today to see how we can support your next project with solutions like vibratory feeders, FIBC big bag discharging stations and more. Call our team of experienced engineers on 01782 567770 or fill out our online enquiry form below.
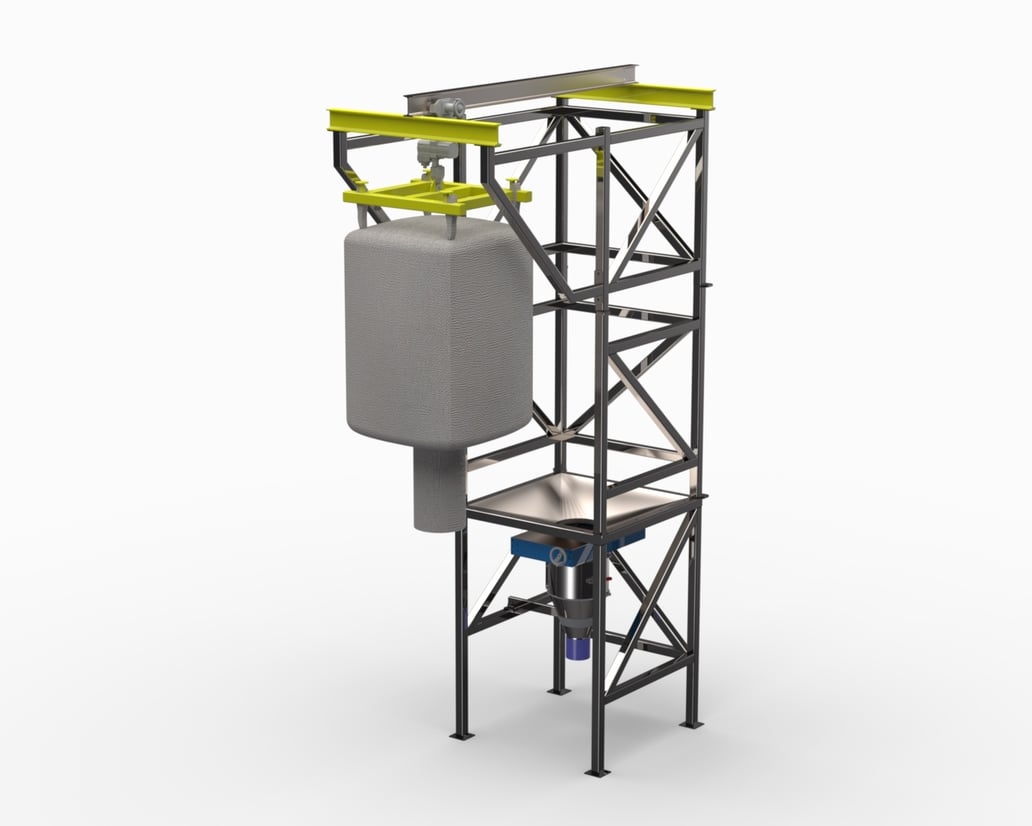