A food producer had used Gough Engineering's reliable and effective machinery for a number of years at multiple sites.
The cereals manufacturer required a turnkey solution incorporating a bucket elevator for material transfer and feeding systems integration.
1. The system required a set of multiple inlet and discharge feeds to integrate into the different production lines and transfer points within the existing factory layout
2. The cereal product required gentle handling with zero product degradation during transfer.
3. Enclosed elevator sections to ensure continuous clean and effective transfer with minimum waste.
4. To design and incorporate heavy duty mechanical components for the potential increase in production volumes.
5. The product being handled was irregular in shape but required carefully controlled feed rates.
Solution
Four Bucket Elevators were commissioned to move a range of cereal products at a rate of 1,000 kgs per hour. The series of Linear Feeders that are fed via Big Bag Stations deposits, feed at a rate of 500 kgs per hour and are also functioned to screen the chocolate coated cereals for abnormally sized pieces of cereal, that can then be fed into a separate system. The interconnecting Conveyor System was nominally set at a speed of 18m per minute.
Result
The Food producer has used Gough Engineering for a number of years at multiple sites as Gough’s reliable and cost effective machinery, accompanied with 24/7 spares and service support, make Gough a safe choice. Gough has many years of handling cereals from sugar coated cornflakes to muesli and oats. As maintaining product integrity and a good flow rate are paramount in the production of cereals, and Gough can ensure both with its range of interfacing materials handling equipment.
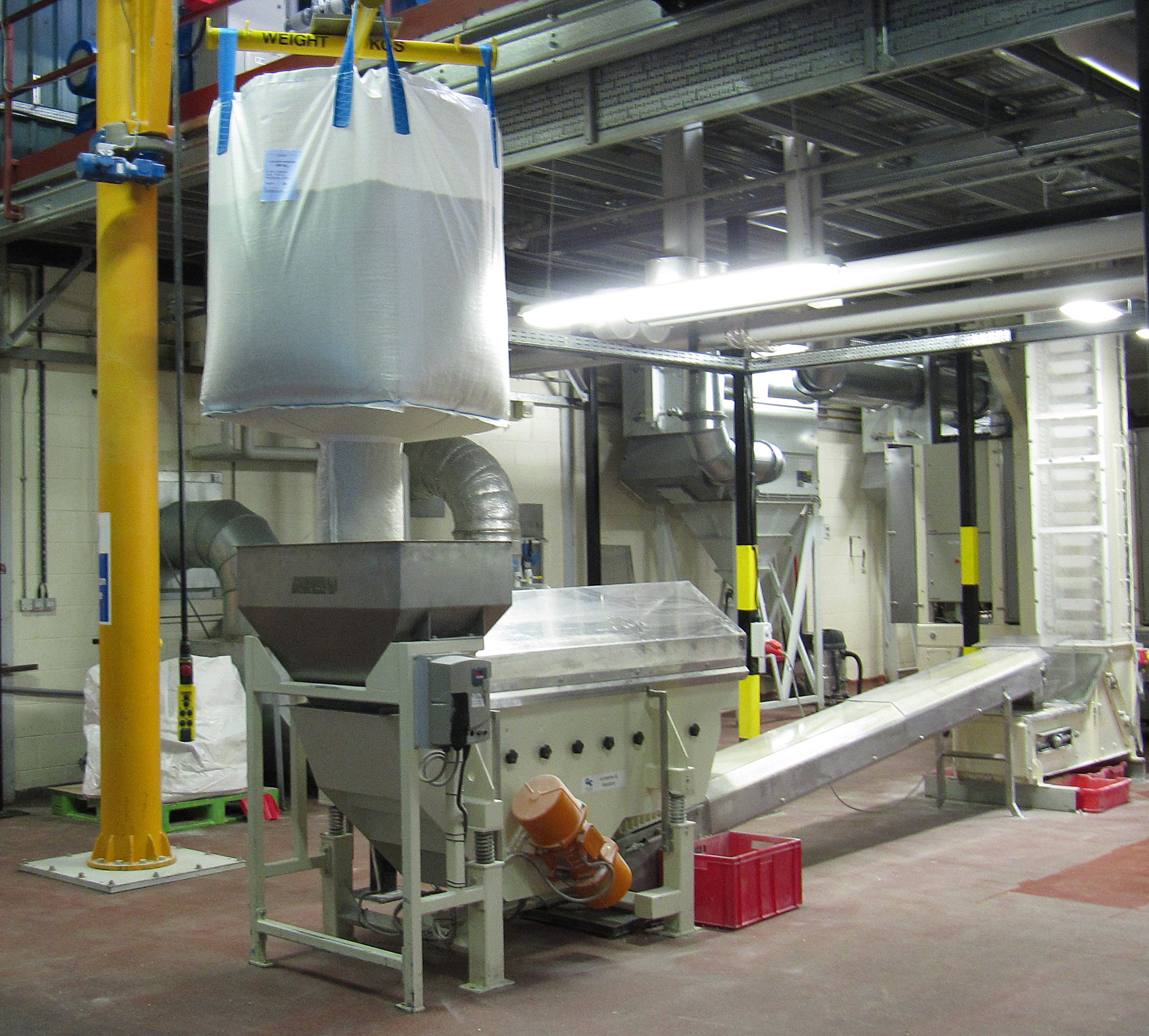
Related Products
Gough Swinglink Bucket Elevator (GBE)
Introducing the configurations and design elements of a bucket elevator, a crucial piece of equipment to move product from one location to another without degrading the product state (suited to all types of fragile product used in the foods, pharma or chemical industries) and ensuring no loss of product as it traverses the required distances - which may require multiple inlets and multiple outlets. The Gough Swinglink solution is the best material handling for food
Vibratory Feeder (GL:VF)
Vibratory feeders allow the controlled movement of product from one location to another using a single tray surface. The vibration can be generated by different drives and is normally required to generate a smooth continuous flow of material from one process to another. If the tray does have a scree built into the tray this would be called a vibratory screen.
Big Bag Discharger (GBB)
The Gough Big Bag Discharger (and also Fillers) are used to reduce the manual handling using small bags (20-25kg) and allows a controlled efficient flow of material from a single or different sizes of big bags. The designs come in many forms for holding the bag as well as the untie chambers and flow control measures Gough can implement.
Parts and Service
The parts and service department has always maintained an excellent client and customer relationship, bringing technical advise as well as the quick supply of spare parts from our in-house stock management.