Dust Extraction & De-dusting
Controlling dust and ensuring air quality is paramount for maintaining a safe and efficient work environment. Managing airborne dust is a significant challenge for industries ranging from food, plastics and recycling to pharmaceuticals and chemicals. It poses serious health risks to workers and can lead to costly regulatory breaches.
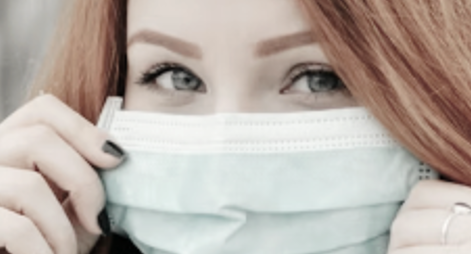
Understanding
Gough Engineering understands the critical importance of maintaining air quality for worker safety, removing unwanted contaminants as well as preventing cross-contamination between different product materials. Contaminants such as metal fragments can lead to major product recalls, damaging reputations and causing substantial financial losses.
Challenges
These challenges necessitate robust material handling solutions that can effectively capture dust and ensure a cleaner, safer workplace. Gough Engineering’s advanced material handling equipment directly addresses these challenges with integrated dust extraction units and cutting-edge metal rejection systems.
Better material handling
Coupled with efficient rip and tip stations, these integrated de-dusting solutions provide:
- Comprehensive dust control through integrated dust extraction units
- Effective air quality management
- Removing cross-contamination
- Prevention of contamination with advanced metal rejection systems
By choosing Gough Engineering’s equipment and support, you can ensure your operations meet the highest standards of safety and quality.
Introduction
Why use rip and tip stations?
Rip and tip stations in material handling are specialised workstations found in many production systems, warehouses and distribution centers.
Rip stations — are dedicated to unpacking incoming goods by opening packages and containers using tools like box cutters, ensuring items are inspected, sorted and sometimes repacked for further processing.
Tip stations — once unpacked, goods are transferred to tip stations where they are tipped onto transfer systems like conveyor belts or sorting systems for efficient movement into further temporary storage or distribution processes.
These stations enhance operational efficiency by streamlining unpacking, improving inventory accuracy and maintaining a safer working environment through dedicated handling and processing areas where manual handling can be improved and safety issues reduced.
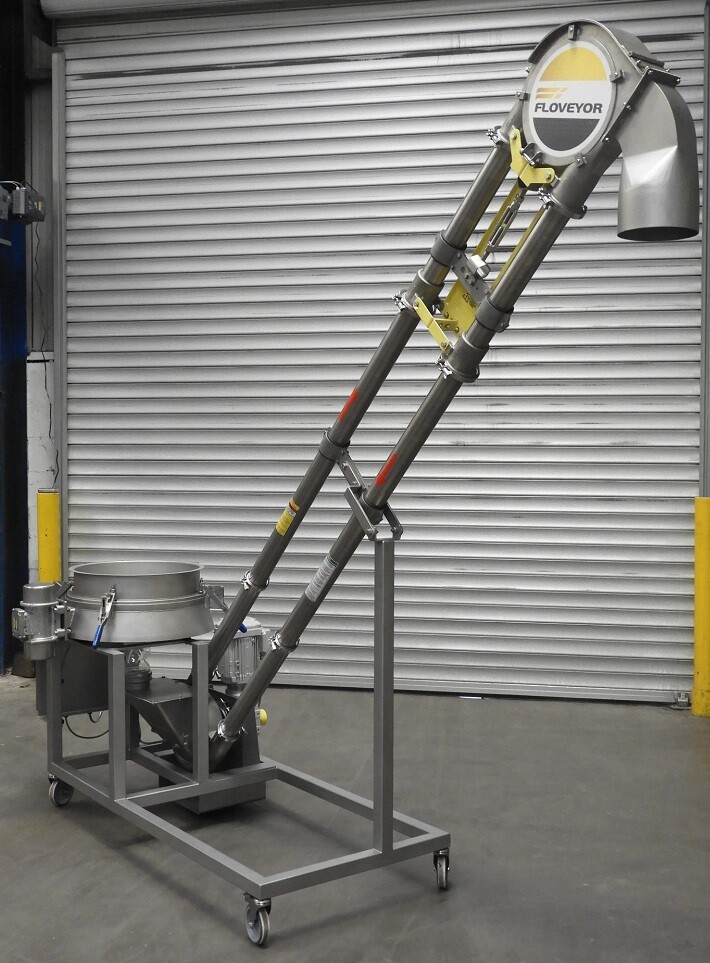
Prevention
Read more on the right on the aspects of dust control with a case study link.
Dust Control
Dust extraction units maintain a clean working environment by capturing airborne particles, improving air quality, reducing respiratory risks and preventing product loss.
Take bucket elevator systems, like Gough’s Swinglink® Bucket Elevator. Adding dust extraction spigots to inlet and discharge points can prevent fine and air-borne powders from spreading. These spigots — openings or outlets that connect ductwork or hoses to equipment — will help contain the powder when it goes in or out of the buckets.
Additional options for vibrational separation machines also include fully enclosed designs using a tubular transfer body design or a removable/ fixed lid.
Integrated extraction can be supplied with a special filter unit, drawing dust from the rip and tip area into a collectable set of enclosed filters. The filters can be cleaned and even removed for cleaning or swap-over to allow the filters to be reused. The objective is to ensure air-borne small particles are removed from the operator’s immediate environment, keeping the machine cleaner throughout a shift.
Read about how Gough engineering’s Vibratory Screens with dust extraction
Contamination prevention
Metal rejection systems detect and remove both ferrous and non-ferrous metal contaminants, ensuring your products are pure and comply with industry standards.
To recover metals such as shredded copper, the Vibrecon® vibratory separator (GVC) is utilised to sort products by particle size using vibration. This equipment features single or multiple decks and is available in various diameters. Employing a gyratory sifting motion, the system consistently processes materials, which enables their reformation, reconstitution, or resale to other manufacturers.
In addition, fixed magnets (or removable) can be fitted to all types of machines to remove ferrous metals.
More sophisticated solutions can also be applied to allow the removable of any ferrous materials automatically, rejected during a gravity-fed situation.
Whatever your requirements, Gough Engineering can review your objectives and design the best solution for your operations.
Reality Case
Gough Engineering’s solutions are not solely for manufacturing processes. The capability of these solutions are exemplified in projects like the development of a mobile single deck linear feeder screen equipped with over-band magnets for the Singapore police force. This bespoke solution efficiently categorises debris and isolates metallic particles, ensuring accurate forensic analysis
The system's effectiveness has expanded its implementation, with adaptations for the Vietnamese and Thai police forces, as well as deployment with the Metropolitan Police Force in the UK, underscoring its broad utility and success.
Contact us today
Want to find out more on our fantastic solutions for extracting dust with our screening equipment...
Call our sales team to discuss your requirements on:
+44 (0)1782 567770
or via email contact@goughengineering.com
Q & A
Here are a few questions and answers and we are always available to call and discuss you application specifics.
Can a sieve be used without a support stand?
Can a sieve have more than one screen?
No, a sieve only has one screen for just 2 fraction separation - same as a Gough Vibraflo (GVF) machine. However, if you need 2 or 3 screens inside one machine then we can supply the Gough Vibrecon (GVC) machine for this type of multi-layer separations. Click here...
What type of mesh aperture sizes do you supply?
What is the best method to deliver to a sieve?
It depends on your delivery process. If you are manually de-bagging say a 25kg bag then a Rip & Tip station with a bag rest area would work well. If you want to empty multiple bags into a hopper, then a vibratory feeder can be useful for this delivery method. Gough supply these units as well. See here...