Rip & Tip Handling Machines
Did you know that 16 percent of food waste in the UK comes from manufacturers and production plants? The Waste and Resources Action Programme (WRAP) figures show that food manufacturers need to optimise their waste handling processes. In doing so, they can minimise waste and ensure product quality and consistency. Consider the challenge of "tramp materials", foreign objects or contaminants that can infiltrate the product stream. These materials range from physical debris like metal fragments, stones, or glass, but also include items such as packaging materials or machinery parts. Tramp materials pose a significant risk to food safety and quality. Their presence can potentially result in contamination, product recalls, or harm to consumers if not promptly detected and removed.
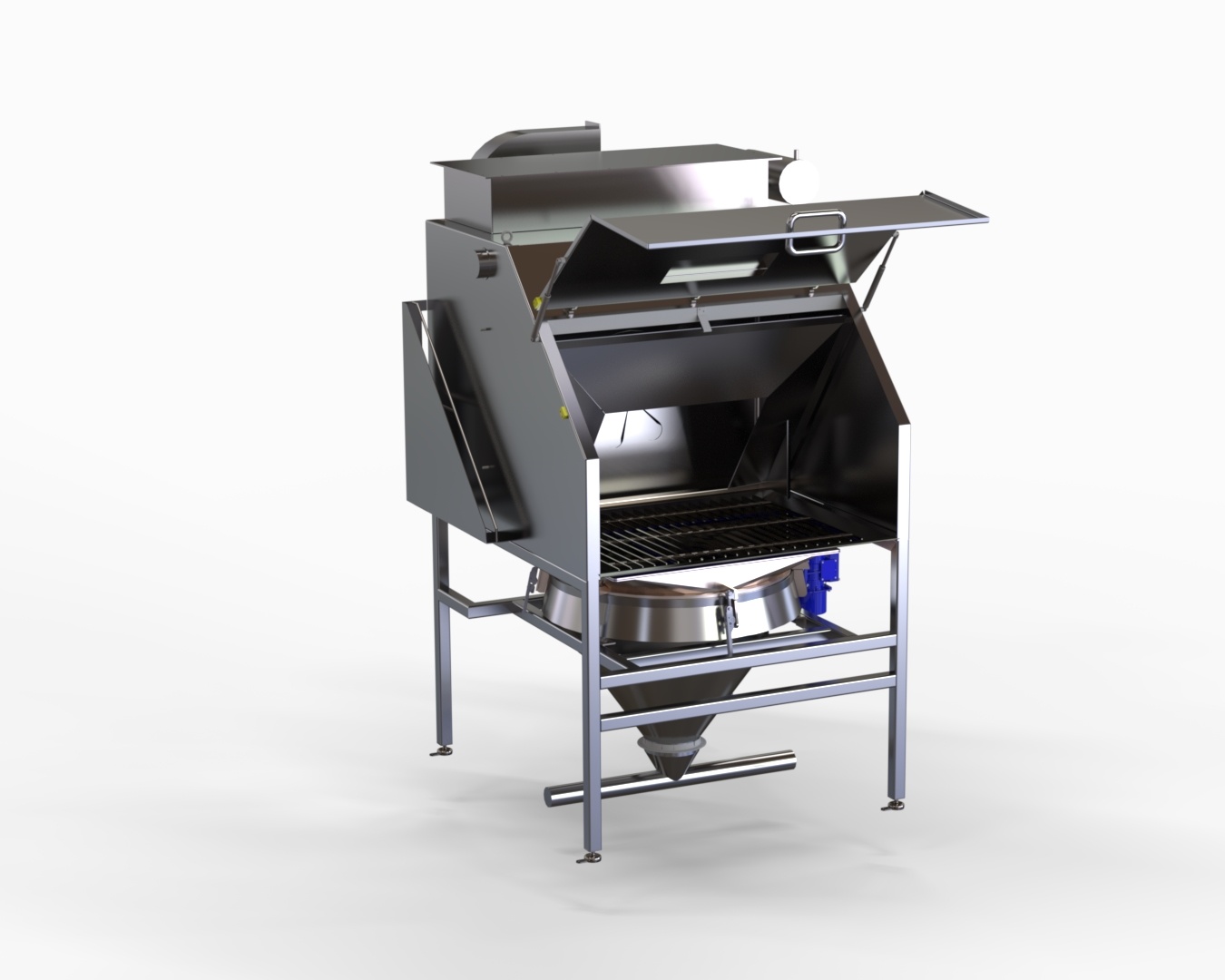
Introduction
Simple & Effective Sieving
Enclosed rip and tip stations provide a contained space for activities, like bag opening and dispensing. These advanced material handling systems prevent foreign objects or contaminants from entering the product stream.
But what factors should you consider before choosing one?
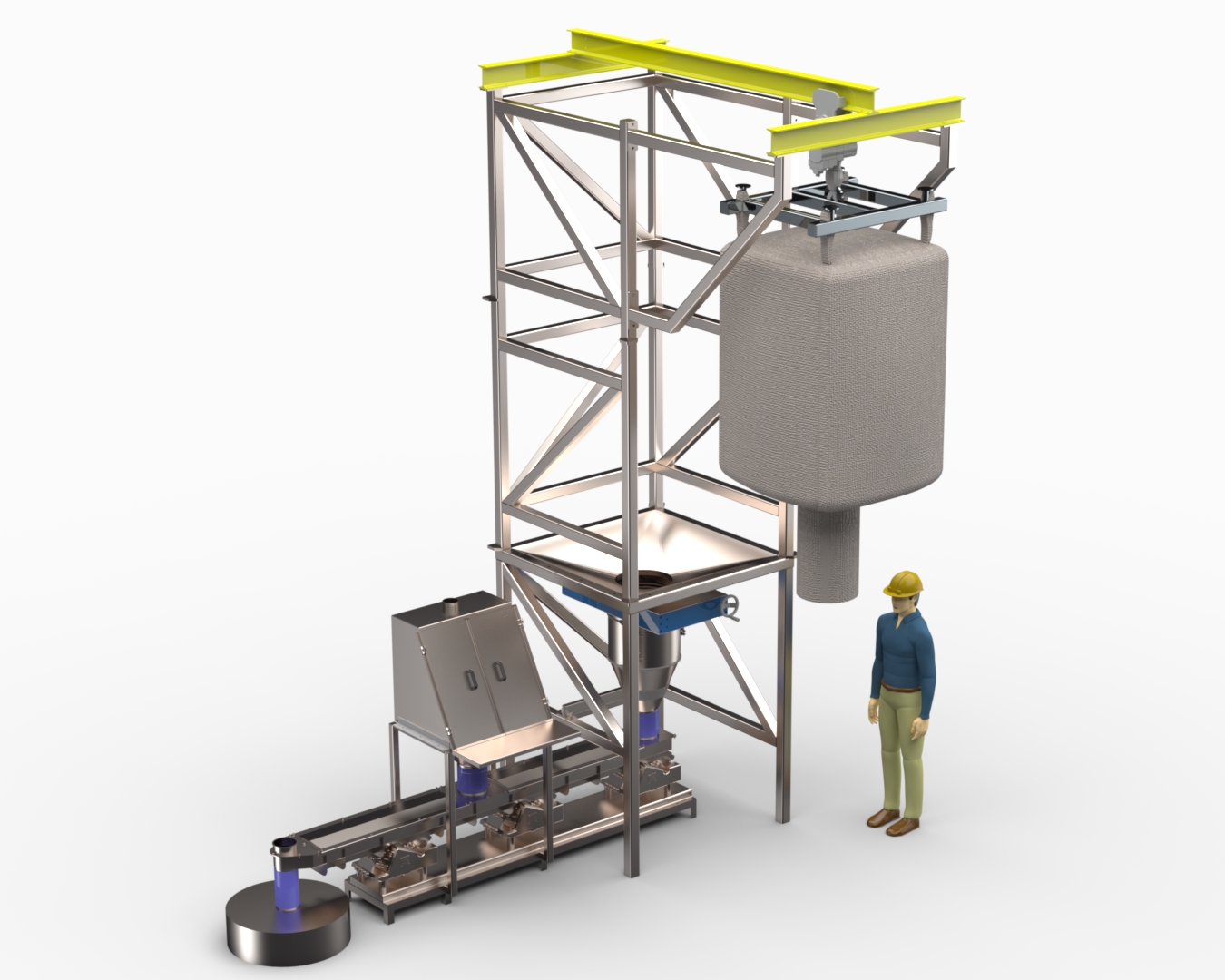
How to choose the right Rip&Tip Station
Identify your requirements
Begin by assessing your specific needs and challenges in your food processing or production environment. You should consider factors, including the volume of bag unloading and the types of materials being handled. Also, what existing quality control measures are in place?
Evaluate containment features
Gough Engineering’s Rip and Tip stations offer effective containment features. The stations are enclosed with sealed compartments for bag opening and dispensing. This prevents contaminants, like tramp materials, from entering the product stream.
Consider dust extraction systems
These integral systems are crucial for removing airborne particles generated during bag unloading processes. Ensure the Rip and Tip station you choose has efficient dust extraction capabilities. This will help maintain air quality and reduce the likelihood of contamination.
Assess screening mechanisms
Gough Engineering’s Rip and Tip stations may include sieves or other screening mechanisms. This further removes unwanted materials from the product stream. Evaluate the effectiveness of these screening features in reducing the risk of tramp materials and enhancing product quality.
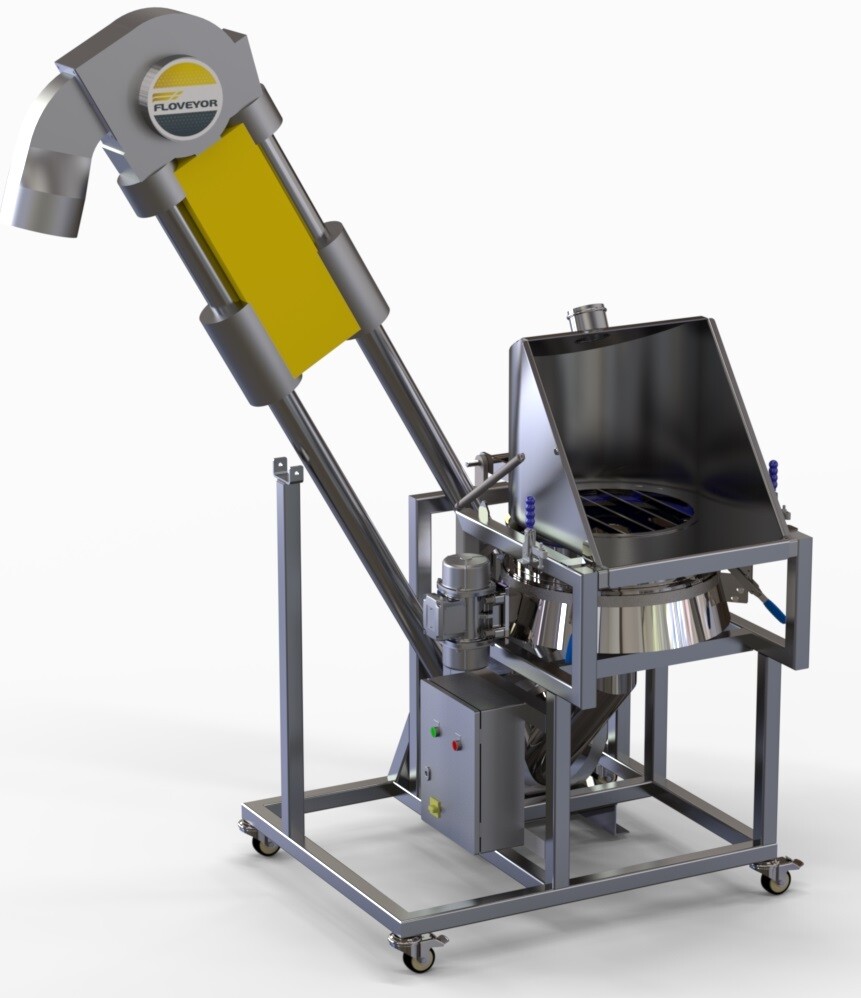
Reality Cases & Articles
Charlie Bigham’s is a manufacturer renowned for its premium ready-to-cook meals. The company wanted to prioritise ingredient quality and air purity in its kitchens.
To address these concerns, Gough Engineering developed a custom enclosed sieving station, the Gough GBS Batch Sieve. Featuring an ATEX-compliant fan and vibratory sieve, this solution ensures efficient screening while containing dust using removable filters for easier hygiene maintenance.
The system is also controlled by a programmable logic controller (PLC). This helps automate manual handling tasks. The result? Consistent screening without compromising air quality.
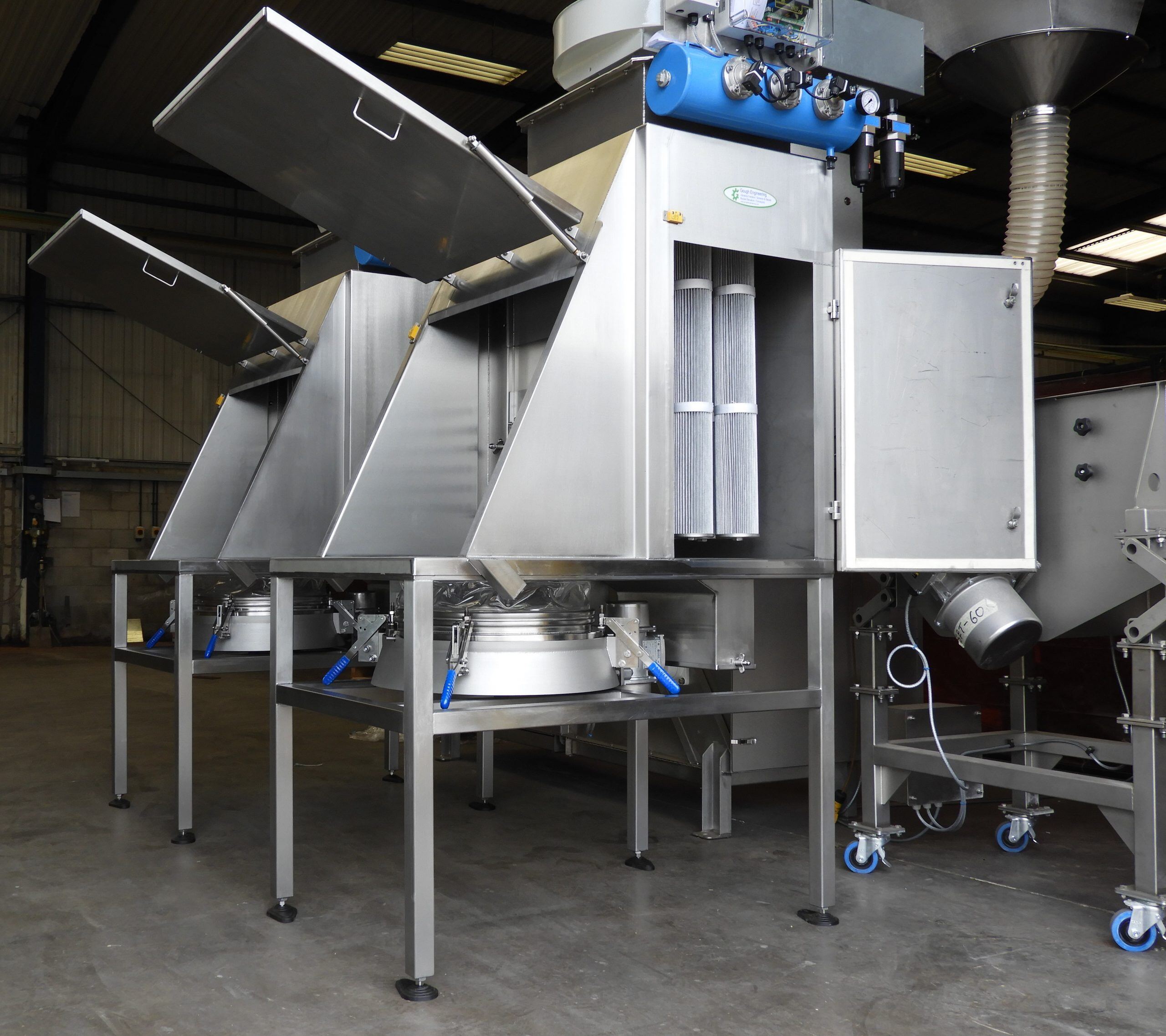
Rip & Tip Station
Easy bag access and cleaning, minimising disruptions to production with an automated material handling solution.
Partnering with Gough Engineering, Charlie Bigham's has automated its processes while maintaining meal quality.
Contact us today
Want to find out more on our wonderful Rip & Tip stations and all its benefits...
Call our sales team to discuss your requirements on:
+44 (0)1782 567770
or via email contact@goughengineering.com