Since early 2018, Gough Engineering has been associated with Floveyor, the original designers of the aero-mechanical conveyor.
This joint venture has enabled us to offer a handling solution specifically designed for conveying powders such as flour.
Chips, Tortillas & Wraps
As part of a push to speed up and improve production, Gough received an enquiry from a food products manufacturer looking for advice on sieving and conveying various ingredients.
The manufacturer is a major supplier of Mexican food items such as chips, tortillas and wraps; with sales across the UK and Europe.
Loading the Mixer Manually
The process for making the tortillas and wraps involves emptying 25kg bags of flour and other ingredients into a mixer.
The mixer is a large industrial unit with an inlet height of over 2,000 mm.
Access to the inlet is via a set of steps and a small platform.
The operators were having to carry the 25 kg bags up the stairs, and lean out over the inlet of the mixer to load the product.
This process creates multiple problems:
- Carrying heavy bags upstairs can be hazardous, leading to health and safety issues
- It is a slow process which ties up operators from other work
- It is strenuous, and only achieved by certain operators
- Emptying the bag directly into the mixer can mean debris, such as pieces of bag and bag string, falling into the mixer leading to reject product, increasing waste and cost.
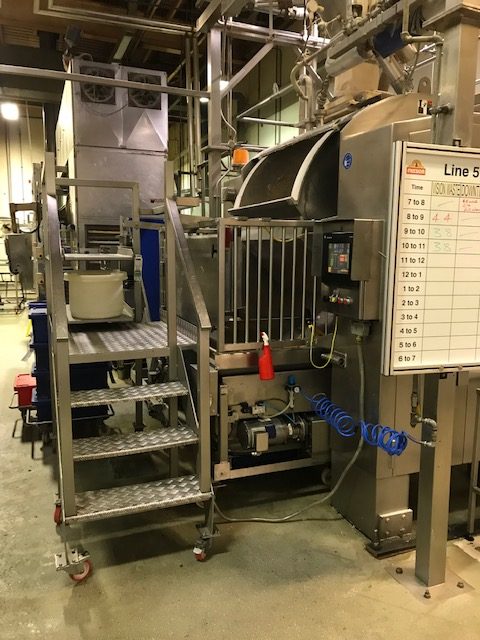
Improving the Process
Having operated in this way, the manufacturer set 3 goals to improve the process:
- Supply a conveying system to allow bags to be emptied at ground level, so operators no longer had to carry the bags up the stairs.
- Include a screening system to prevent debris reaching the mixer.
- Make the whole system mobile, so the system could be used to load multiple mixers.
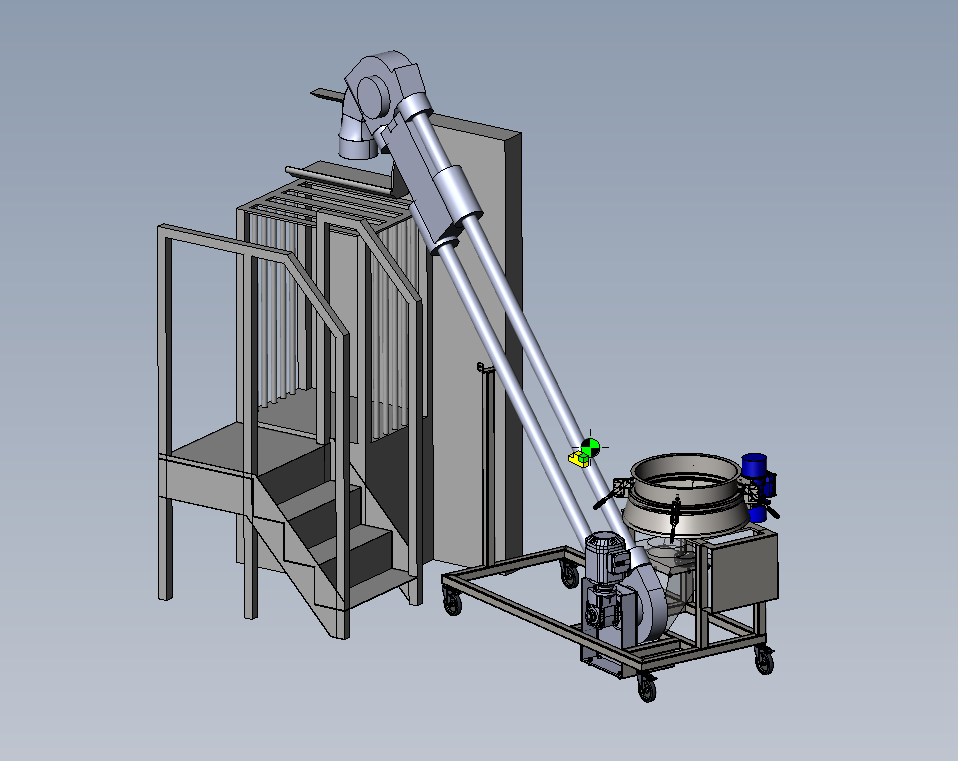
The Equipment Solution
After consideration of the various options, a system including a vibrating batch sieve, Floveyor aero-mechanical conveyor, and mobile support frame was supplied.
Now, operators open and empty the sacks into the vibrating sieve at ground level.
The sieve filters out any debris, and sieved flour empties into the inlet of the aero-mechanical conveyor.
The sieve connects to the inlet of the aero-mechanical conveyor by an airtight flexible connection, ensuring no spillage or waste.
The aero-mechanical conveyor moves the flour along a stainless-steel pipe before discharging into the open inlet of the mixer.
The system enables the mixer to be loaded with the specified ingredients in less than 4 minutes.
While the mixer is processing, the conveying system can be wheeled into position to load the next mixer.
Customer Evaluation
Since putting the first system to work, the customer has ordered 2 more units to feed mixers on a new production line.
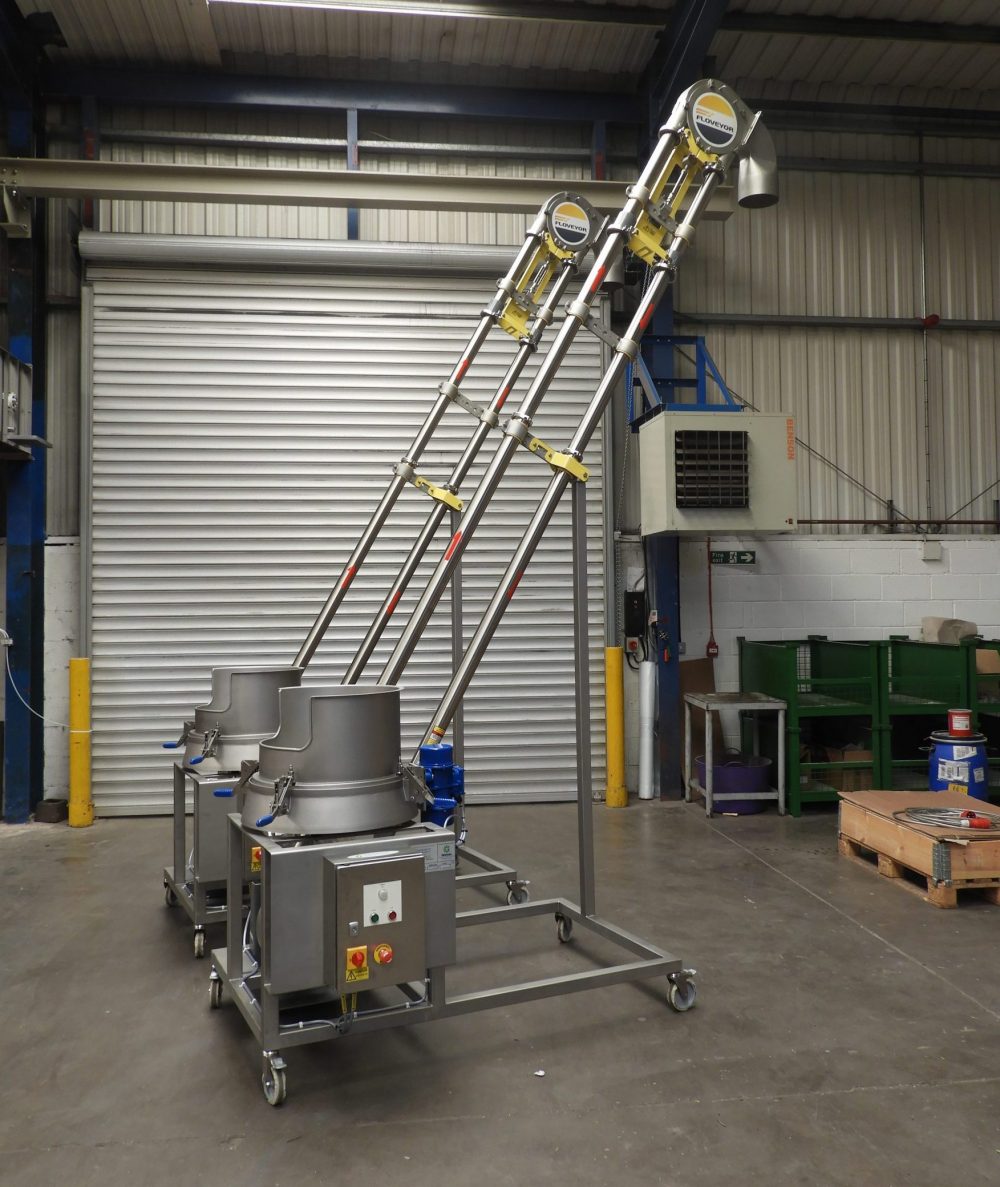
Follow our LinkedIn page for more examples of improving product handling in a range of industries.