There are many ready-to-cook food producers in the market place, however Charlie Bigham’s stands head and shoulders above the rest for producing delicious dishes that are as good as home cooked. Using high quality ingredients and recipes, Charlie Bigham’s meals are sold through Waitrose and other supermarkets, as well as under their own label. With each meal being lovingly handmade, automation within the production process is, naturally, limited. However, recently a need arose at the Charlie Bigham’s food production campus in north London to screen powdered products that have arrived in bag form, ensuring that the Charlie Bigham’s chefs could continue to cook with the confidence that their ingredients were of the highest quality.
Maintaining air quality within a kitchen environment
Charlie Bigham’s approached Gough Engineering Ltd with a request for a system that could provide high quality screening whilst maintaining the air quality of the kitchen. As they have no requirement for an air extraction system within their production kitchens, the routine solution of installing an air extraction pick-up point above the sieve was ineligible.
In order to contain any air borne dust generated during the bag opening and dispensing phase and meet with the relevant HSE requirements for Control of Substances, Gough Engineering Ltd. designed an enclosed rip and tip sieving station with integral dust extraction system as an innovative alternative.
A custom-designed solution featuring an ATEX compliant integral fan
The freestanding station incorporates a vibratory sieve alongside an access and containment hood with hinged closure. Gough Engineering Ltd. then designed an in-built dust extraction, capable of expelling the clean air into the surrounding environment.
The “Rip and Tip” sieving station is accessed by opening a hinged front door within the hood enclosure, which is supported by gas struts. Bags are placed on support bars above the vibratory sieve before being opened and tipped. The custom designed unit is constructed entirely from stainless steel, with 316 used for product contact areas and all other areas in 304L grade.
The hood enclosure includes an ATEX compliant integral fan assisted dust extraction unit complete with reverse air jet cleaning facility incorporating a number of removable pleated cartridge filters. The extraction unit is sized to take any airborne product up and through the cartridge filters prior to ejecting the air, ensuring no dispersal of particles into the surrounding workspace.
Controlled via a small PLC, which includes adjustable timer functions for both dust extraction and the compressed air filter cleaning cycle, the vibratory sieve is based on Gough Engineering Ltd.’s successful range of batch sieves, and uses a single out of balance motor to provide the vibratory motion for efficient and consistent product screening. A bespoke and simple drop-in mesh design allows easy access and removal of the mesh ring, enabling quick cleaning for product changeover and causing minimum disruption to production processing.
Gough Engineering Are Here To Help
To find out how Gough Engineering could help your manufacturing business with a customer design solution, call our expert team in the office on +44 (0)1782 567770 or click here to complete our online enquiry form
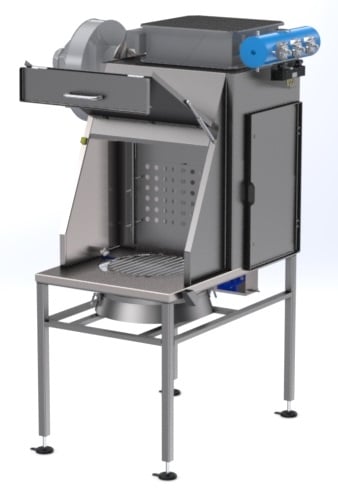