For over 3 years, Gough Engineering have been developing and refining a bespoke linear screening system for a major customer (who we won’t be naming in this article), who is one of the largest manufacturers of chocolate products in the world.
Since originally supplying a system to a site in the UK, 4 more have been sent to sites across Europe, with a 5th project soon to be finalised.
Our Customer – International Chocolate Supplier
The company group is split into 3 region operations (EMEA, The Americas, and Asia Pacific) and a globally managed cocoa business, organised from a head office in Switzerland.
It operates out of 62 factories worldwide; employ over 12,000 people; and despatches over 2 million tonnes of products a year, generating $7.4 billion in revenue in 2018.
According to the company’s website, its chocolate is present in 1 out of every 4 chocolate and cocoa products consumed around the world.
Its passion for chocolate, and a desire to supply only high-quality products, lead directly to the development of the new linear screening process.
Requirements
The company supplies chocolate drops in various sizes, to confectioners around the world. The drops are bagged and despatched to the confectioners, who use the drops as an ingredient for their final products. The confectioners melt the drops down, and mix in other ingredients ready for moulding into whatever form they need.
‘Functional Requirements’
The ‘functional specifications’ as described by the customer were simple:
Sieves [screens] are used to separate and classify solid product.
The required output of the system was defined as:
product will be separated/classified into fines, usable product and lumps. Fines and agglomerates [lumps] are reject.
Usable Product and Rejects
A variety of sizes of chocolate drops are produced by the manufacturer.
To process the various sizes, a selection of removable and replaceable screening plates were supplied with the system, with the appropriate plates being included as needed.
Fines and Lumps
Fines and lumps are to be rejected.
To save waste they are recycled through the process.
Fines are small pieces that have been chipped off the chocolate pieces during the conveying process. Lumps are pieces of product that have stuck together.
The Purpose of Screening
Fines and lumps need are removed for multiple reason.
At the most basic, sending product to customers with lots of clumps and broken pieces mixed in gives the impression of a low value product, no matter how good it tastes.
From a practical manufacturing perspective, fine particles will build up inside processing equipment, increasing cleaning requirements, so it is best to remove as many as possible to reduce manufacturing costs.
Lumps are removed as they affect the customers’ final product.
For the best results, the drops need to melt evenly and completely.
As lumps are larger than the individual drops, they take longer to melt. Modern, high volume food production relies on careful timing. If the pre-set melting time of an automated production system isn’t long enough to melt the lumps, they won’t mix properly with any ingredients added to the chocolate, and will lead to an inconsistent final product.
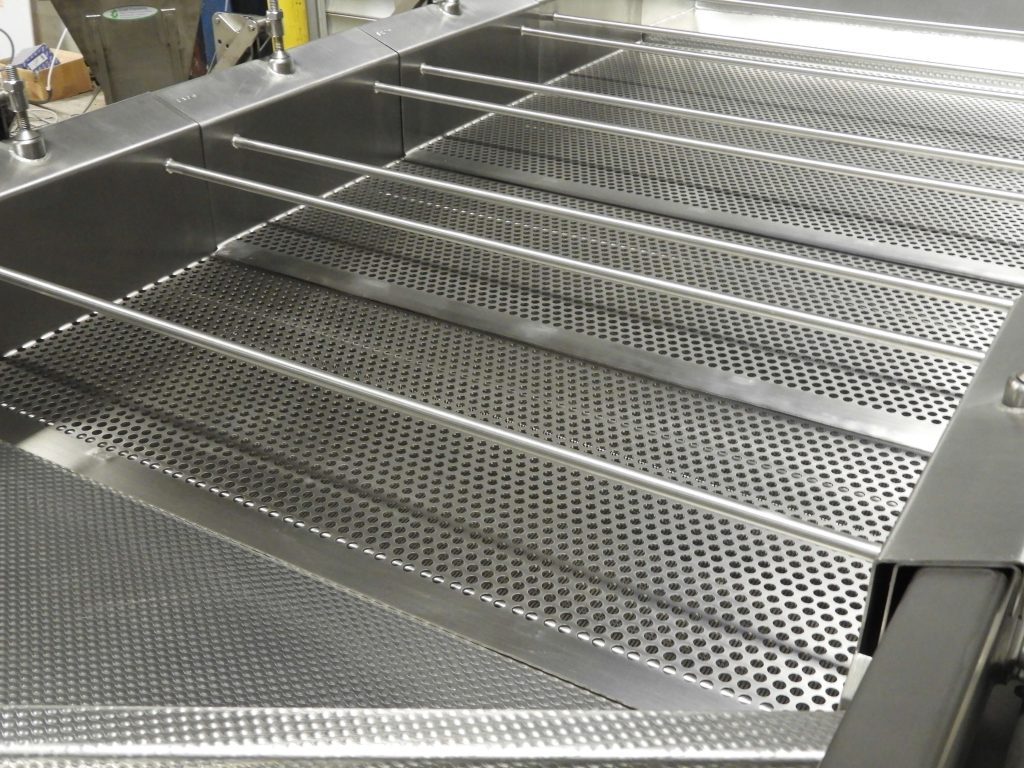
Screening Process
The screen was positioned between a cooling conveyor and the packing systems.
The conveyor fed product onto the inlet end of the screen.
Lumps are separated by the top screening plate.
The plate aperture is chosen to contain oversize lumps, which carry on to the top outlet. Anything smaller falls through, which includes usable product and fines.
The usable product and fines then move across a smaller aperture screening plate. This time usable product is contained, and only fines fall through. The usable product continues on, discharging onto a conveyor which transfers product to the packing systems.
Fines move to a separate outlet below for collection and reprocessing.
Screening System Development
The development of the system has taken place over 3 years.
Over that time, 4 individual screening systems have been supplied to different sites across Europe.
Each has had incremental improvements applied, refining the system to make it more relevant to the particular issues arising from handling the particular products.
Along with some dimensional changes, and reorganising of outlets to work with existing conveying equipment, perhaps the most significant development has been the use of rigidised stainless steel plate on the surfaces making contact with the product.
When the first system was put into production, it was noticed that fats released from the product were building up on the flat surface at the bottom of the screen tray. This was not only something that required extra cleaning, but product was actually sticking to the bottom of the tray.
Including the rigidised tray, which has a wave pattern, meant the contact area between the chocolate and the tray was greatly reduced. This reduced the amount of smearing of product on the tray, and greatly reduced the build-up.
This rigidised pattern has since been included on all system supplied.
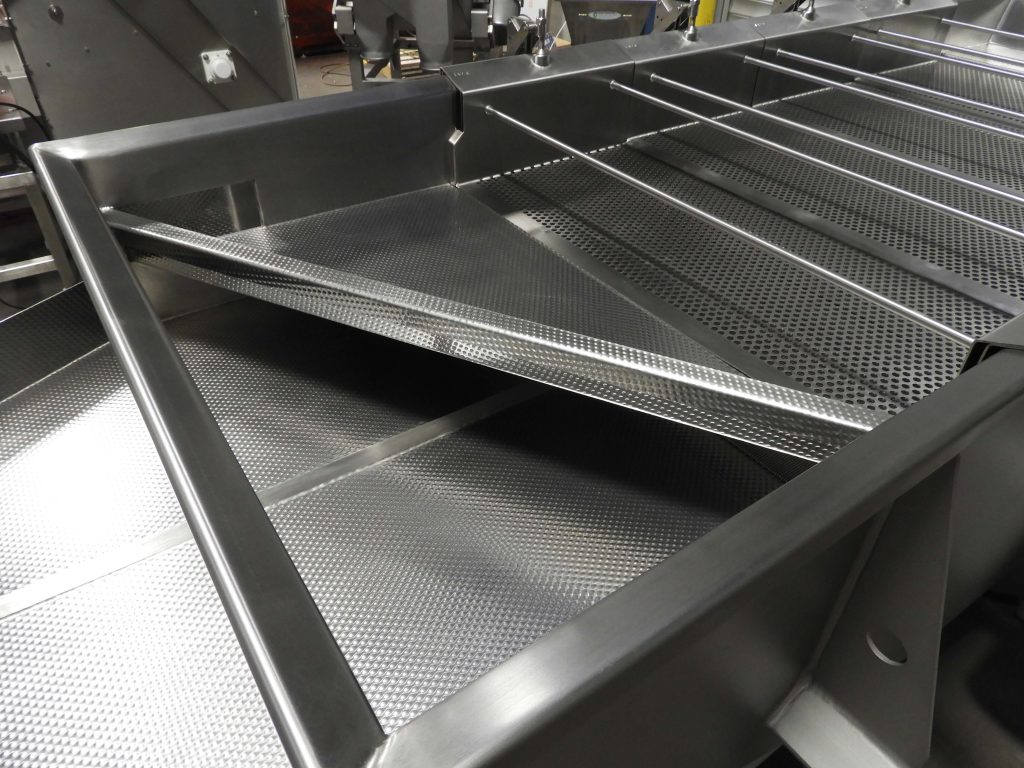
Screening System Specification
The final system specification was an all grade 304L stainless steel, 2 deck system.
Designed to screen 3,600 kg of product (500 – 800 kg / m3) per hour, the system was made 900 mm wide to make the screen section large enough to allow the throughput.
Each screening deck was split into 4 sections, each less than 12.5 kg, to allow for easy handling and fast replacement.
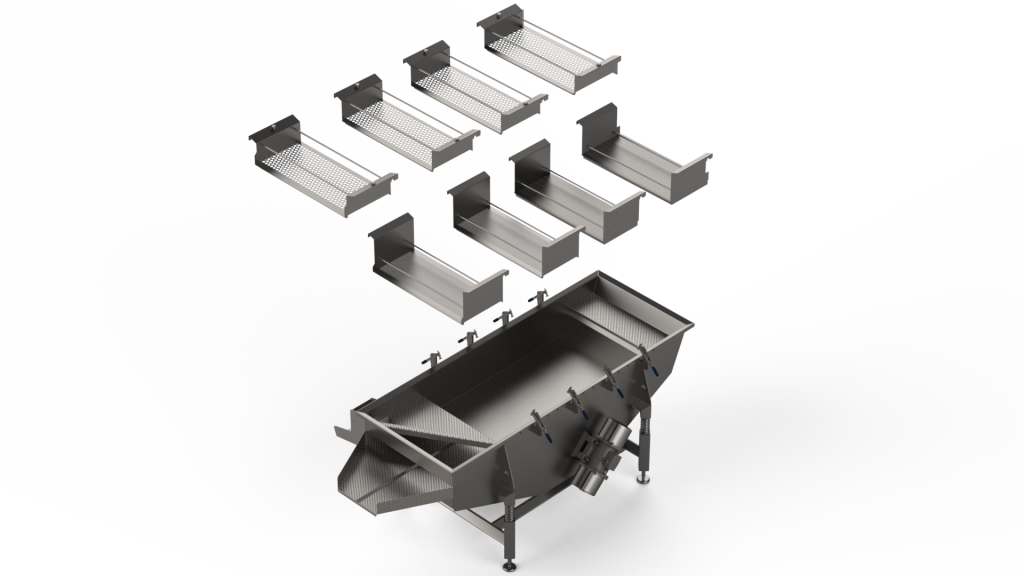
The screen apertures ranged from 37 mm to 10 mm on the top deck, while the bottom deck included options of a 4 mm diameter plate, or a 1 mm aperture wedge wire screen for separating fines from the smallest products.
The system vibrates at 25Hz, and an amplitude of 4 mm, driven by twin eccentric motors.
For easy clean down, all internal corners were manufactured to a minimum of 3 mm radius, so any residue can be wiped out quickly.
Follow our LinkedIn page for more examples of improving product handling in a range of industries.