Particle size distribution (PSD) refers to a list of values used to illustrate the relative amount of particles sizes in a sample of a particulate product. Once the required particle size is finalised for a specific particulate product, trials are carried out to determine the appropriate equipment to achieve the desired results at production scale. This equipment is then used to achieve a consistent particle size, and, as a result, the finished product will exhibit the required characteristics and properties.
Established in 1940, Gough Engineering manages products and ingredients within production processes, and has provided vital equipment to national and international companies. Our screening solutions are built upon an in-depth understanding of the importance of removing out of specification (oversize and undersize) particles from the target product.
However, before we discuss this equipment, we’ll discuss the importance of PSD data, highlight how it benefits a range of sectors, and outline the test methods required to obtain PSD data.
Why is particle size distribution data important?
- PSD data is paramount in determining the level of active pharmaceutical ingredient (API) within pharmaceutical manufacturing processes.
- PSD data is monitored in many food production processes – particle size distribution can have an impact on the final product’s taste and appearance.
- PSD data is vital for assessing material performance, particularly within civil engineering (such as the strength and load bearing capabilities of soil and rocks).
Pharmaceutical manufacturing and PSD
Process engineers within the pharmaceutical industry pay particular attention to PSD within material samples. As briefly mentioned above, fluctuations in particle size can result in unwanted changes to the finished product – such as the proportion of the drug present within an individual’s circulation (and therefore its ability to have an active effect) and the stability of the final item on the shelf (shelf stability). Prior to the manufacturing process, each individual drug is allocated its particle size range as well as other values such as particle surface characteristics. In terms of particle size, a narrow distribution range is desired (the drug is closer to its target specification when a narrow distribution range is present).
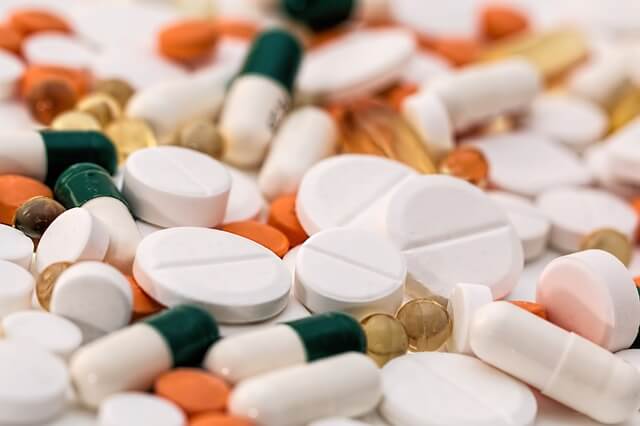
Particle size distribution in food and beverage applications
During the manufacturing process of many food and beverage items, obtaining a narrow particle size distribution is vital. The properties of the food can be negatively impacted if this is not achieved (for example, the taste and the consistency). Food and beverage items where this is of particular importance include:
- Powders (such as flours, herbs, spices, dried products, tea, and coffee)
- Pellets (such as pellets. grains, pet foods, meals, beans, and crumbs)
- Emulsions (such as edible oils)
- Suspensions (such as extruded snacks – flakes and shapes)
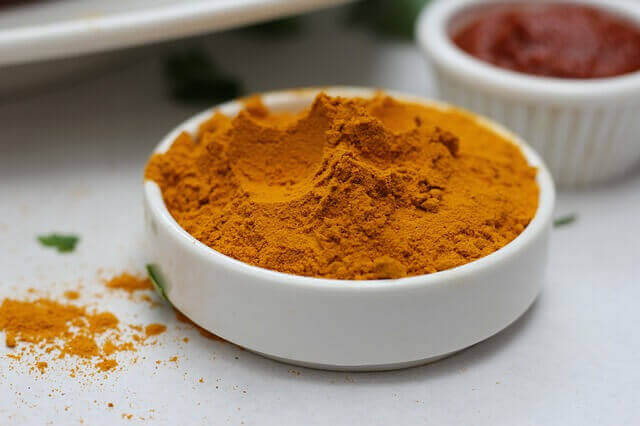
The importance of particle size in polymers
The size and shape of particles, for example plastic pellets used in injection moulding processes, can greatly affect the outcome of the finished product. No matter what the resin type is, pellet size and shape should be perfectly uniform to ensure that pellets are melted at a consistent rate. On top of this, very small particles (fines) melt quicker and cause an inconsistency in not only the colour but the properties of the product. In this manner, PSD ultimately affects the overall quality of the moulded parts.
The size of polymer particles is also important for the lifespan of the manufacturing equipment. Larger pellets can create blockages or cause the machine to malfunction. At best, production is slowed or stopped while the equipment is cleaned. Over time, however, equipment fails which is costly to repair or replace.
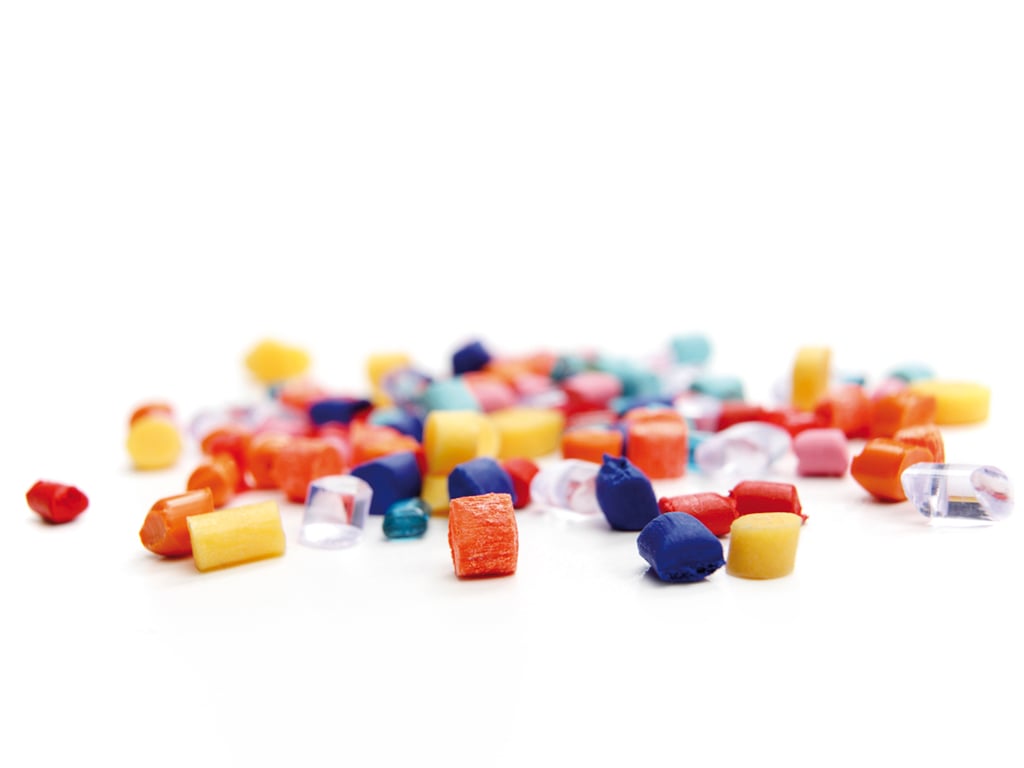
How are particle sizes measured?
A number of techniques are available to size particles, determine the range, and the average particle size. Particle size analysers are used (PSAs), such as:
- Analysis of Brownian motion
- High definition image processing
How is particle size distribution assessed?
To obtain particle size distribution data, sieve analysis is often employed (this is often referred to as a gradiation test). During analysis, sample material is passed through a series of sieves. As the material moves through the sieves, the mesh size decreases. The level of material collected at each level is then weighed and the tester is able to see what proportion of the entire mass of material has been effectively “held up” at each level. A breakdown of particle size can then be provided to the relevant stakeholders for analysis. If PSD is in line with the tester’s requirements, the next step is to achieve a consistent particle size distribution at scale.
Achieving a consistent particle size distribution at scale
Achieving a consistent particle size distribution at scale is important – however, the cost effectiveness of the method must also be considered. To gain an understanding of costs and provide tailored recommendations, trials are carried out. At Gough Engineering, these trials enable us to state the number of tonnes per hour that can be processed (and at what cost).
Following trials, we provide the appropriate screening and sieving material. Recent examples include:
Screening a lime catalyst: Our client required a solution to enable them to achieve an accurate particle size during the manufacturing of air filtration equipment. In order to provide enough surface area to achieve the desired reaction required to remove CO2, it was necessary that the particles were of a certain size. If the material included large lumps, the surface area would be too small. If the particles were not large enough, air would not be able to pass through the gaps at the required rate.
Screening a breakfast cereal: Our client required a solution to achieve a consistent texture of a popular rice based breakfast cereal. Without this consistency, the final product would not meet consumer expectations.
Read about our sieves, screens and separators – Gough has developed solutions for a range of production processes within food production, chemicals and pharmaceuticals, recycling product recovery, and plastics.