When planning a product handling system one of the most important factors to consider is the throughput capacity of the system.
As bucket elevators are a key part of many of these systems, it is important to be able to accurately calculate the potential throughput capacity of any bucket elevator being considered for the project.
Types of Bucket Elevator
There are two main different types of bucket elevator. One is a belt & bucket elevator which uses buckets fixed to a belt, these systems run at high speeds and are able to achieve high rates of product throughput (100s of cubic metres per hour) but are not suitable for all product applications as they can damage product. The way they work involves a lot of kinetic energy, and the system literally throws the product out of the outlet using centrifugal force. This type of system is also limited to a fixed speed (otherwise the centrifugal discharge action won’t work) and to only having one product inlet and one product outlet. They are generally cheaper but are obviously not suitable for every product handling scenario.
The other type of bucket elevator, the type of bucket elevator offered by Gough Engineering, uses buckets that are mounted between two parallel chains which allow the buckets to hang like a pendulum with the product resting in the bottom. To discharge the product from the bucket, the buckets are tipped using a cam at the desired location. The system is slower, and is not capable of throughput rates above 30 cubic metres per hour, but does allow multiple product inlets and outlets giving great flexibility with factory layout, and offer gentle product handling with less spillage.
The Factors That Affect Throughput Capacity
The volumetric throughput capacity of a bucket elevator is dependent on the following factors:
- Bucket Capacity – This is the total volume of product that can be held within each bucket. A caveat to this is that a bucket will have a maximum working volume, usually around 65% of the overall volume, to minimise spillage because of overfilling and prevent excessive swinging. For an example calculation below we’ll use the units cubic metres (m3).
- Bucket Pitch – This is the distance between the centres of each bucket. For calculation purposes, we need to think of this figure in terms of distance per bucket (m/bucket) or we can flip that over to the number of buckets per metre (buckets/m).
- Bucket Speed – The rate at which the buckets are travelling (m/minute).
Combining these factors gives the total volumetric bucket capacity moving through the system, which equals the volume of product that can be conveyed.
Example Calculation
We can think of the throughput capacity as the rate that the buckets move past the inlet (and subsequently the outlet which will be the same). We have used some round figures below for a simple example calculation:
Bucket speed = 15 m/minute, bucket pitch = 0.25 m/bucket (or 4 buckets/m), bucket working volume = 0.005 m3 (or 5 litres)
15 m/minute x 4 buckets/m = 60 buckets/minute
Substituting in the bucket working volume we get:
0.3 m3/minute of volumetric throughput capacity
As the product handling industry work using throughput capacity per hour, we can multiply that figure by 60 (60 minute per hour) to give:
18 m3/hour
How to Calculate for Different Products
At the beginning of a project we will ask a customer ‘What product throughput rate do you need to achieve with this conveying system?’. The answer is usually a figure given using the units tonnes per hour.
Bucket elevators handle a huge variety of product from crisps to cement mix, and all these products have different densities. When we start talking about tonnes per hour instead of volume per hour in relation to throughput, the density of the product becomes important, and must be factored into the calculations.
Fortunately, it is a very simple calculation to make. All we need to do is multiply the volumetric throughput capacity by the bulk density of the product. Most of the time the customer will know the bulk density, if not, we can take a sample of product, divide the mass by the volume, and calculate to get a figure that can be given using the units tonnes/m3.
So, assuming a product bulk density of 0.2 tonnes/m3 (an approximate figure for crisps), and continuing from our previous example:
18 m3/hour x 0.2 tonnes/m3 = 3.6 tonnes/hr
For a quick comparison, we can also run the calculation for a product with a much higher density. Assuming a bulk density of 1.3 tonnes/m3 (an approximate figure for cement mix) we get:
18 m3/hour x 1.3 tonnes/m3 = 23.4 tonnes/hr
From this example, we can see how the exact same elevator can deliver very different masses of product depending on the product’s density.
All these calculations can be handled by Gough Engineering at the beginning of a project, and we can offer our knowledge and experience to advise on all the other complexities of specifying and installing a product handling system. We have a range of bucket sizes, along with other product handling equipment to deal with most product and throughput requirements.
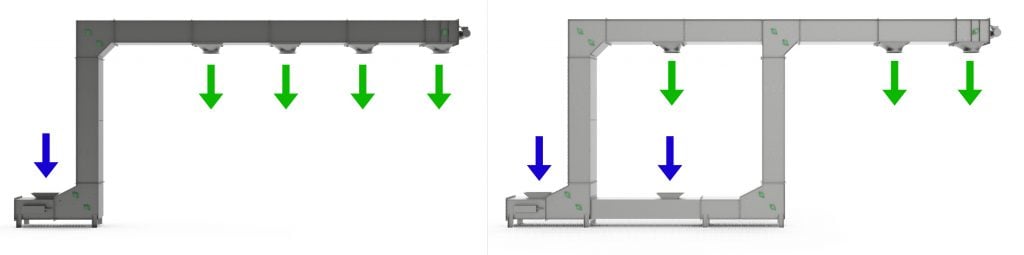
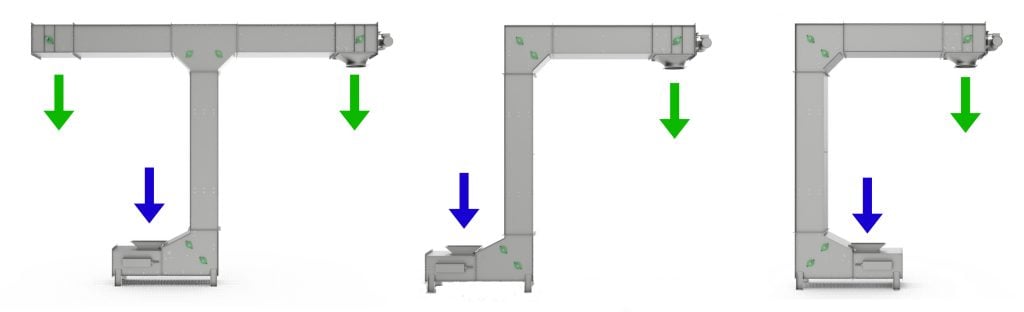
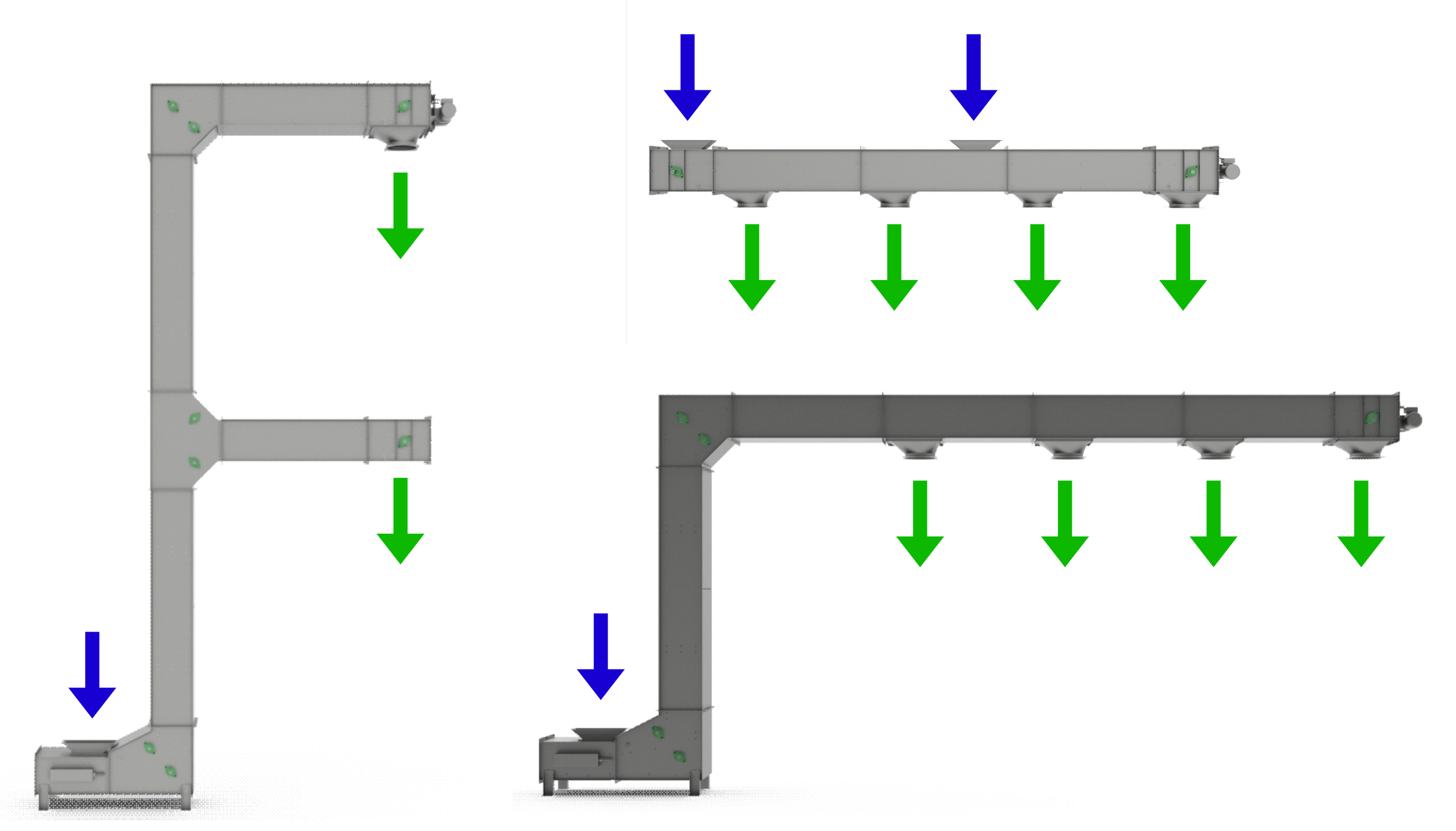