According to the Intergovernmental Panel on Climate Change (IPCC), food waste and loss contribute to about eight-to-ten per cent of the world's total greenhouse gas emissions, equivalent to emissions from cars. The urgency to reduce waste falls not only on consumers but also on food manufacturers, as every sector must play its part in addressing climate change. Here, Stephen Harding, managing director of Gough Engineering, delves into the role of bucket elevators in the food manufacturing industry, focusing on how Gough Engineering's Swinglink® 9" bucket elevator supports waste reduction, enhances efficiency and promotes safety.
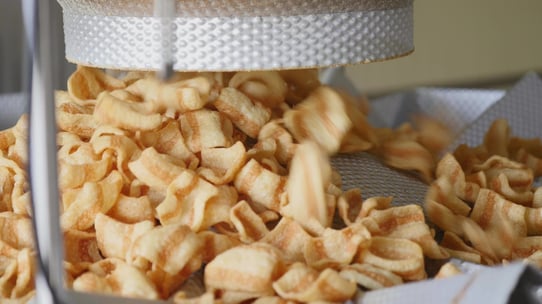
Traditional belt and bucket elevators tend to be fast and aggressive in scooping up materials from the bottom or boot section and throwing them out at the top. Unfortunately, such processes can cause breakage or degradation of fragile products. A gentle and smooth handling approach should instead be employed, where materials are poured into the buckets at a controlled rate. Gentle handling is particularly crucial for preserving the integrity of delicate products like crisps.
That is why the performance and throughput of a bucket elevator are essential considerations for food manufacturers, and should be tailored to the manufacturer’s specific material handling needs. The throughput is calculated in terms of tons or kilograms per hour, ensuring efficient movement of materials without degradation. By selecting the appropriate bucket size, manufacturers can optimise throughput, ensuring smooth operations on the production line.
Design flexibility
To this end, manufacturers should opt for bucket elevators that have design flexibility, allowing for customisation to meet varying production environments and layouts. With the ability to add more buckets and extend the chains, the bucket elevator can seamlessly adapt to changing production requirements. Modular designs are especially useful, as they allow easy extension should a manufacturer wish to expand their production line in the future.
Pendulum designed bucket elevators allow the buckets to move with minimal waste or spillage. The pendulum effect, achieved through two pins on either end of the bucket, ensures the bucket's orientation remains constant during movement. Unlike other bucket elevators that experience overspill as they elevate materials, this design ensures the product remains within the bucket throughout the process.
Gough Engineering has delivered successful bucket elevator solutions across various industries. They include its Swinglink® bucket elevator, a highly efficient and gentle handling solution for material transportation. Unlike traditional belt and bucket elevators, the Swinglink® system offers controlled, smooth movement, reducing product degradation and waste. The buckets are designed to retain the product securely, minimising spillage and ensuring little to no wastage between buckets.
Preventing spillage
Gough Engineering's Swinglink® bucket elevator maintains the product's shape and form from the bottom to the elevated position. At speeds around 15 meters per minute, the bucket design ensures there is no waste during the material's journey through the elevator. Moreover, the elevator's unique design prevents spillage between buckets, minimising waste and the need for frequent clean-ups during the feed process.
The elevator can also be designed with many different configurations, with multiple feed entry points and multiple discharge points to convey material correctly within the production processes. The product route can also be configured in many ways, from a simple ‘Z’ shape to more complicated step or ‘C’ shapes.
The elevator's pendulum design allows the buckets to remain in the same orientation, preventing product damage during elevation. The system is customisable with various bucket sizes and materials, including stainless steel and metal detectable options, and adaptable to different production layouts, and can be easily extended or reconfigured as production needs change. During the cabin 3D modelling stages, there is significant back and forth communication with the customer to finalise the designs. Gough Engineering specialists make every effort to gather all necessary information from the outset, especially regarding lengths and heights for material transfer.
One Gough Engineering customer, a major supplier of nuts and cereals in West London, needed to repackage bulk products into smaller sizes. They were using an old bucket elevator that caused frequent breakdowns and couldn't cope with increased demand after upgrading their weighing and bagging processes.
Gough was assigned to replace it with a Swinglink® bucket elevator, offering higher throughput and better control feedback. The new elevator also accommodates the existing infeed vibratory feeder with improved operator access and product loading. As a result, the client can now increase production output to meet customer demand, and synchronise with downstream processes. Additionally, the elevator's speed and function can be effectively monitored through the supplied control system.
In the quest to reduce food waste and greenhouse gas emissions, food manufacturers must embrace sustainable practices. Gough Engineering's Swinglink® 9” bucket elevator presents a powerful solution for reducing waste, enhancing efficiency, and promoting safety in the food manufacturing industry.